Method for manufacturing laminated strip-shaped LED backlight modules
A technology for a backlight module and a manufacturing method, which is applied to the manufacturing field of a laminated strip LED backlight module, can solve the problems of limited heat dissipation efficiency, inability to reduce the number of use, lack of process design, etc., so as to improve the packaging quality and reduce the cost. Effect
- Summary
- Abstract
- Description
- Claims
- Application Information
AI Technical Summary
Problems solved by technology
Method used
Image
Examples
Embodiment Construction
[0038] Please cooperate first figure 1 As shown, the first embodiment of the manufacturing method of the laminated strip LED backlight module of the present invention, the manufacturing method of the laminated strip LED backlight module 1 of the present invention mainly includes the following steps: providing a clean room A working space; a strip graphite substrate 10 is provided; a top surface of the graphite substrate 10 is coated with an insulating adhesive film layer 20; at least one group of electrode wires 30 is fixed on the surface of the insulating adhesive film layer 20; several LEDs The chips 40 are arranged along the electrode wires 30, and the diodes of each LED chip 40 are electrically connected to the electrode wires 30 by bonding wires 41, and then the surface of the LED chips 40 is coated with a fluorescent agent 50; Form an encapsulation layer 60 on the outside of the LED chip 40 by pressing B; install and fix the strip-shaped lens 70 on the surface of the enc...
PUM
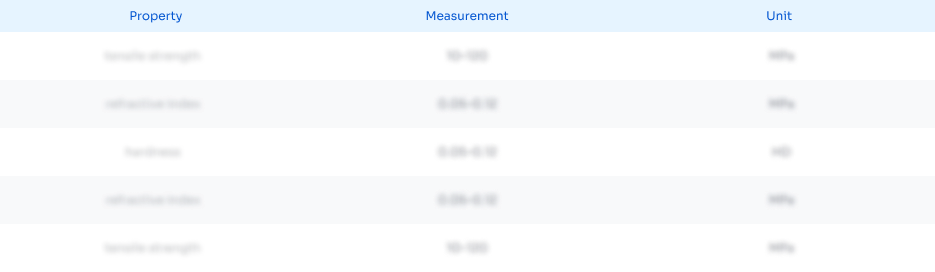
Abstract
Description
Claims
Application Information

- Generate Ideas
- Intellectual Property
- Life Sciences
- Materials
- Tech Scout
- Unparalleled Data Quality
- Higher Quality Content
- 60% Fewer Hallucinations
Browse by: Latest US Patents, China's latest patents, Technical Efficacy Thesaurus, Application Domain, Technology Topic, Popular Technical Reports.
© 2025 PatSnap. All rights reserved.Legal|Privacy policy|Modern Slavery Act Transparency Statement|Sitemap|About US| Contact US: help@patsnap.com