Salinization treatment process for smoke dust of flash furnace and device thereof
A treatment process and treatment device technology, applied in chemical instruments and methods, dispersed particle separation, separation methods, etc., can solve the problems of difficult removal of waste heat boilers, flue corrosion, aggravation, etc., to reduce the occurrence rate of smoke and dust, and prevent sticking. effect on objects and corrosive flues, increasing the chance of collision
- Summary
- Abstract
- Description
- Claims
- Application Information
AI Technical Summary
Problems solved by technology
Method used
Image
Examples
Embodiment Construction
[0018] The present invention will be described in detail below in conjunction with the accompanying drawings.
[0019] figure 1 It is a schematic structural diagram of a flash furnace fume salinization treatment device of the present invention, and the flash furnace is mainly used for smelting sulfide concentrates such as copper and nickel. Such as figure 1 As shown, the flash furnace fume salinization treatment device can be used in flash smelting furnace or flash converting furnace, such as figure 1 As shown, the device includes a base 14 for installation on the inner wall of the furnace, a spray gun 4, an oxygen mixing pipeline 3, a normal oxygen pipeline 1 for feeding oxygen-enriched air and a pure oxygen pipeline for feeding industrial pure oxygen 2. One end of the spray gun 4 is inserted and fixed on the base 14 through the furnace wall, and a nozzle is provided in the middle. The angle between the nozzle and the central axis of the furnace body is 30-90 degrees. For e...
PUM
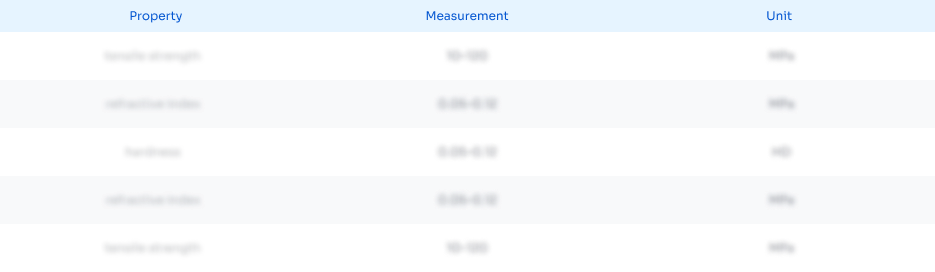
Abstract
Description
Claims
Application Information

- R&D Engineer
- R&D Manager
- IP Professional
- Industry Leading Data Capabilities
- Powerful AI technology
- Patent DNA Extraction
Browse by: Latest US Patents, China's latest patents, Technical Efficacy Thesaurus, Application Domain, Technology Topic, Popular Technical Reports.
© 2024 PatSnap. All rights reserved.Legal|Privacy policy|Modern Slavery Act Transparency Statement|Sitemap|About US| Contact US: help@patsnap.com