Method for manufacturing elastic foam by using reclaimed wastes as materials
A technology of elastic foaming and waste, which is applied in the field of elastic pads, can solve the problems of time-consuming and manpower waste, air or water pollution, environmental protection, etc., and achieve the effect of reducing the cost of recycling, reducing the amount of garbage, and omitting the use
- Summary
- Abstract
- Description
- Claims
- Application Information
AI Technical Summary
Problems solved by technology
Method used
Image
Examples
Embodiment 1
[0036] Such as figure 1 and Figure 2a to Figure 2d As shown, in the preferred embodiment 1 of the present invention, the elastic foam method using recycled waste as a material, the first step is recycling 100: the waste containing materials such as rubber, plastic, fiber and metal is recycled, Such as footwear such as sports shoes.
[0037] The second step of the present invention is shredding 110: using a known shredder 10 to shred the waste (sports shoes) into pieces. After the recovered waste is chopped into chips, although there are still impurities that cannot be completely separated, the chips with different components can be added to the foam material as secondary raw materials. Among them, the rubber material is mainly used for waste Plastic scraps can be used as elasticity adjustment materials for foaming raw materials, waste scraps mainly made of plastic materials can be used as hardness adjustment materials for foaming raw materials, and waste scraps mainly fiber...
Embodiment 2
[0046] Such as image 3 As shown, it is the elastic foam method using recycled waste as material in the preferred embodiment 2 of the present invention, and the multi-layer cushion body with different physical properties and softness and hardness characteristics can also be made according to the method of the present invention. The difference of the above-mentioned preparation method mainly lies in implementing the following steps between the tablet pressing and foam molding steps:
[0047] Softening treatment 160: heating the surface of the sheet-shaped foam material at a temperature of 150° C. to 250° C., or applying a surface softener to the surface of the sheet-shaped foam material for softening treatment.
[0048] Attaching the surface material 170: placing a surface material on the surface of the sheet-shaped foam material and applying pressure so that the two are relatively attached. The surface material can be the same as or different from the sheet foam material, suc...
PUM
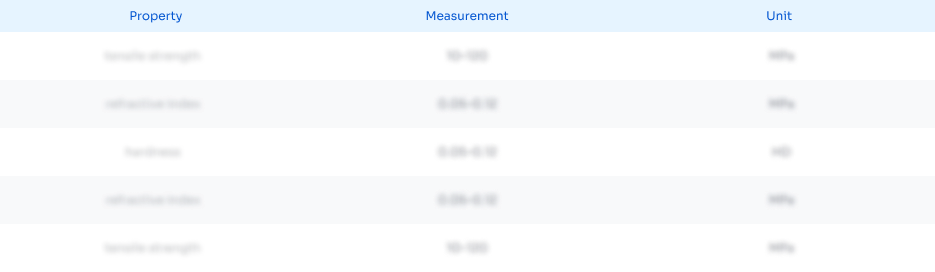
Abstract
Description
Claims
Application Information

- R&D Engineer
- R&D Manager
- IP Professional
- Industry Leading Data Capabilities
- Powerful AI technology
- Patent DNA Extraction
Browse by: Latest US Patents, China's latest patents, Technical Efficacy Thesaurus, Application Domain, Technology Topic, Popular Technical Reports.
© 2024 PatSnap. All rights reserved.Legal|Privacy policy|Modern Slavery Act Transparency Statement|Sitemap|About US| Contact US: help@patsnap.com