Fuselage structural component of an aircraft or spacecraft, with a foam layer as thermal insulation
A technology of structural components and foam layers, applied to aircraft parts, fuselage, fuselage bulkheads, etc., can solve the problems of reduced actual weight advantages and increased weight of CFK structures, and achieve the effects of simplifying cost savings and preventing condensation
- Summary
- Abstract
- Description
- Claims
- Application Information
AI Technical Summary
Problems solved by technology
Method used
Image
Examples
Embodiment Construction
[0032] exist figure 1 A fuselage structural component 1 according to the invention is shown in detail in . The fuselage structural part 1 , which can be formed, for example, as a shell part or fuselage cylinder, has an outer shell or outer shell plate 2 and an inner frame structure 3 , in particular an inner shell or inner shell plate 3 . Said fuselage structural element 1 is then connected to the aircraft fuselage by means of rivets or other suitable fastening means, as known in the prior art. In this case, at least one foam layer 4 is arranged between the outer shell 2 and the inner shell 3 . The foam layer 4 is fastened on the outer shell 2 and / or the inner shell 3 by, for example, bonding.
[0033] Such as figure 1 As shown, the fuselage structural component 1 has an inner shell 3 forming a frame 5 . In this case the inner shell 3 can be formed as a one-piece lining, wherein the inner shell 3 can consist, for example, of a single piece of CFK prepreg. Optionally, the ...
PUM
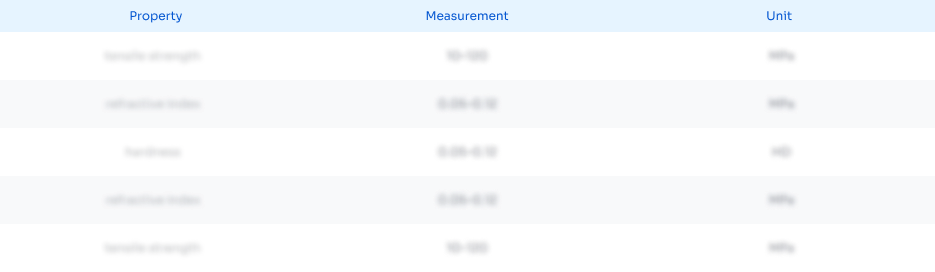
Abstract
Description
Claims
Application Information

- Generate Ideas
- Intellectual Property
- Life Sciences
- Materials
- Tech Scout
- Unparalleled Data Quality
- Higher Quality Content
- 60% Fewer Hallucinations
Browse by: Latest US Patents, China's latest patents, Technical Efficacy Thesaurus, Application Domain, Technology Topic, Popular Technical Reports.
© 2025 PatSnap. All rights reserved.Legal|Privacy policy|Modern Slavery Act Transparency Statement|Sitemap|About US| Contact US: help@patsnap.com