Anti-flooding assistant, preparation method thereof and use thereof
An additive and color-floating technology, used in textiles, papermaking, fiber processing, etc., can solve the problems of shrinkage, pinholes, poor anti-floating effect, and incompatibility between additives and polyurethane. good color effect
- Summary
- Abstract
- Description
- Claims
- Application Information
AI Technical Summary
Problems solved by technology
Method used
Image
Examples
Embodiment 1
[0038] Embodiment 1 prepares anti-floating auxiliary agent
[0039] The solvent-based polyurethane resin slurry obtained in Reference Example 1 was diluted with a mixed solvent of DMF and MEK (mass percentage DMF:MEK=80:20) to a solid content of 15% and a viscosity of 4 Pa.s. Add 0.1 mol of IPDA and 0.2 mol of cyclohexylamine, stir at 1000 rpm for 10 minutes, add 0.2 mol of IPDI dropwise after stirring evenly, and prepare tetraurea after 15 minutes of dripping, among which IPDA, cyclohexylamine and IPDI The ratio of the total mass of the solvent-based polyurethane resin to the mass of the non-volatile components contained in the solvent-based polyurethane resin slurry was 1:5, and then stirred and reacted at a speed of 1000 rpm for 30 minutes, and the reaction temperature was room temperature 25°C. Tetraurea was prepared, unloaded for use. Take 515g of the sample, slowly add 5g of white carbon black (gas phase) at a stirring speed of 1000 rev / min, stir and disperse for 30min,...
Embodiment 2
[0040] Embodiment 2 prepares anti-floating auxiliary agent
[0041] The operation steps are the same as in Example 1, select 0.2mol of benzylamine, 0.1mol of ethylenediamine and 0.2mol of IPDI to react, and drop IPDI in 15min, wherein the total mass of benzylamine, ethylenediamine and IPDI is mixed with the solvent The mass ratio of the non-volatile components contained in the type polyurethane resin slurry was 1:5, and then stirred at a speed of 1000 rpm for 30 min, and the reaction temperature was room temperature 25°C. The diurea was obtained, and the material was unloaded for use. Take 515g of the sample, slowly add 5g of white carbon black (gas phase) at a stirring speed of 1000 rev / min, stir and disperse for 30min, then use a three-roll mill to grind and disperse 3 times, and use a scraper fineness meter to test the When the fineness of the sample is less than or equal to 5 μm, the material is discharged for use, and sample 2# is obtained. In the obtained samples, poly...
Embodiment 3
[0042] Embodiment 3 prepares anti-floating auxiliary agent
[0043] The operation steps are the same as in Example 1, select 0.2mol of benzylamine, react with 0.2mol of HDI, and finish adding HDI dropwise in 15 minutes, wherein the total mass of benzylamine and HDI is the same as that of non- The mass ratio of the volatile components was 1:5, and then stirred at a speed of 1000 rpm for 30 min, and the reaction temperature was room temperature 25°C. The diurea was obtained, and the material was unloaded for use. Take 515g of the sample, slowly add 5g of white carbon black (gas phase) at a stirring speed of 1000 rev / min, stir and disperse for 30min, then use a three-roll mill to grind and disperse 3 times, and use a scraper fineness meter to test the When the fineness of the sample is less than or equal to 5 μm, the material is discharged for use, and sample 3# is obtained. In the obtained samples, polyurethane, polyurea, silica, BHT, BYK-9565, and PCD accounted for 79.0%, 15....
PUM
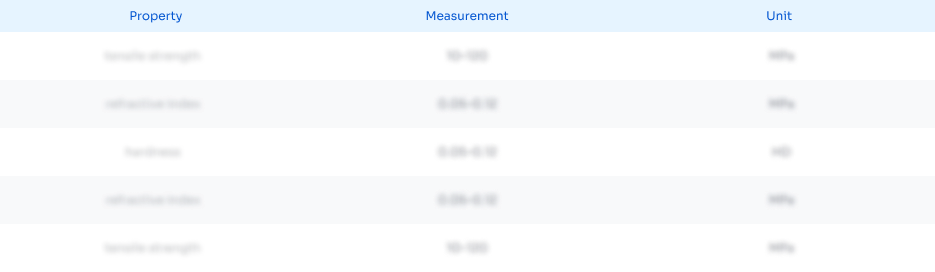
Abstract
Description
Claims
Application Information

- R&D
- Intellectual Property
- Life Sciences
- Materials
- Tech Scout
- Unparalleled Data Quality
- Higher Quality Content
- 60% Fewer Hallucinations
Browse by: Latest US Patents, China's latest patents, Technical Efficacy Thesaurus, Application Domain, Technology Topic, Popular Technical Reports.
© 2025 PatSnap. All rights reserved.Legal|Privacy policy|Modern Slavery Act Transparency Statement|Sitemap|About US| Contact US: help@patsnap.com