Application of micro-capsule self-repair technology in automobile brake shoe made of composite material
A technology of composite materials and brake pads, which is applied in the application field of microcapsule self-repair technology in composite automobile brake pads, can solve problems such as poor wear performance and high noise, and achieve the elimination of safety hazards, vibration reduction and noise reduction performance Good, the effect of prolonging the service life
- Summary
- Abstract
- Description
- Claims
- Application Information
AI Technical Summary
Problems solved by technology
Method used
Image
Examples
Embodiment 1
[0015] Embodiment 1, the composite material of the novel composite material automobile brake pad that contains self-healing microcapsules is made up of following material (by weight percentage): Nano-modified resin 10.8%, composite mineral fiber 18.1%, organic fiber 6%, Mineral fiber 3%, ceramic fiber 5.3%, artificial graphite 6.5%, barite 8%, diatomaceous earth 4.5%, chromite powder 3.6%, potassium feldspar 3.8%, zircon 2.2%, antimony sulfide 3.2% , expanded frog stone powder 3.6%, iron black 1.8%, aluminum powder 4.2%, mica 3.1%, coke powder 2.2%, nitrile rubber powder 3.5%, tire powder 4.6%, zeolite 1.2%, polyurea formaldehyde coated dicyclopentadiene Diene (DCPD) microcapsules 0.8%.
[0016] Mix the above materials evenly; put them into the die of the vulcanizing machine for hot pressing, the pressing temperature is 170°C±10°C, the pressing pressure is 14MPa±0.5MPa, keep the heat and pressure for 15 minutes, and press it into brake pads; put the brake pads into the power ...
Embodiment 2
[0021] Embodiment 2, the composite material of the novel composite material automobile brake pad that contains self-repairing microcapsule is made up of following material (by weight percentage): 9.6% of nano-modified resin, 19.6% of composite mineral fiber, 7.2% of organic fiber, Mineral fiber 2.6%, ceramic fiber 4.2%, artificial graphite 7.5%, barite 7.6%, diatomaceous earth 2.5%, chromite powder 4.4%, potassium feldspar 2.8%, zircon 3.2%, antimony sulfide 2.6% , expanded frog stone powder 5.6%, iron black 3.2%, aluminum powder 3.0%, mica 2.1%, coke powder 2.8%, nitrile rubber powder 2.5%, tire powder 2.8%, zeolite 1.8%, polyurea formaldehyde coated dicyclopentadiene Diene (DCPD) microcapsules 2.4%.
[0022] Mix the above materials evenly; put them into the die of the vulcanizing machine for hot pressing, the pressing temperature is 190 °C ± 10 °C, the pressing pressure is 16 MPa ± 0.5 MPa, heat preservation and pressure for 12 minutes, and press into brake pads; put the bra...
PUM
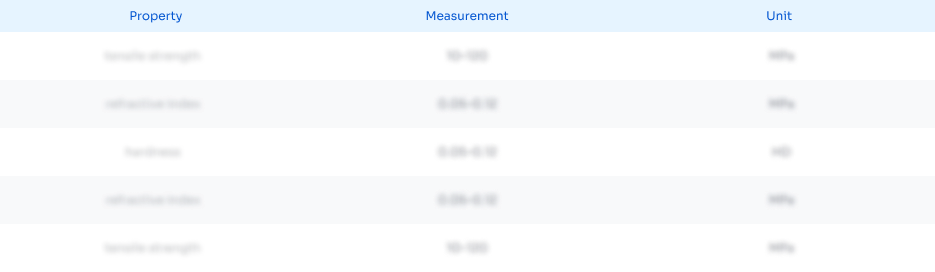
Abstract
Description
Claims
Application Information

- R&D
- Intellectual Property
- Life Sciences
- Materials
- Tech Scout
- Unparalleled Data Quality
- Higher Quality Content
- 60% Fewer Hallucinations
Browse by: Latest US Patents, China's latest patents, Technical Efficacy Thesaurus, Application Domain, Technology Topic, Popular Technical Reports.
© 2025 PatSnap. All rights reserved.Legal|Privacy policy|Modern Slavery Act Transparency Statement|Sitemap|About US| Contact US: help@patsnap.com