Co-extrusion preparation method of polymer functionally gradient materials (FGM) and products
A technology of gradient functional materials and polymers, applied in the field of polymer material processing, to achieve the effect of simple process and easy control
- Summary
- Abstract
- Description
- Claims
- Application Information
AI Technical Summary
Problems solved by technology
Method used
Image
Examples
Embodiment 1
[0026] Embodiment 1: High-density polyethylene (HDPE) and polyoxyethylene (PEO) are weighed respectively by the mass percentage of 75:25, add the feeding device of SHJ-20B twin-screw extruder after fully mixing by mixing machine, extrude The temperature of the discharge barrel is set and controlled at 110-185°C from the solid conveying section to the melt conveying section (exit) [the outlet temperature is set according to (T 2 +T 1 ) / 2 setting]; the shaping mold is a fishtail sheet mold designed and manufactured by the inventor, and the mold is composed of an upper and lower mold body and is insulated with a heat insulating material, wherein the temperature T of the upper mold body 1 Set and control at 160°C, while the temperature of the lower die body T 2 Set and control at 210°C, the ΔT=T formed in the cavity of the extrusion mold 2 -T 1 = 50°C temperature gradient field; the extruder extrudes a 0.5mm thick molten sheet at a speed of 300mm / min, and then passes through a ...
Embodiment 2
[0027] Embodiment 2: Weigh polymethyl methacrylate (PMMA), polyoxyethylene (PEO) and functional additive carbon black (CB) respectively by the mass percentage of 55: 45: 1.5, add after fully mixing by mixing machine The feeding device of the IMC-1663 single-screw extruder, the temperature of the barrel of the extruder is set and controlled at 110-205°C from the solid conveying section to the melt conveying section (exit); the upper and lower mold bodies of the shaping mold are insulated The material is insulated, where the temperature of the upper die body T 2 Set and control at 230°C, while the temperature of the lower die body T 1 Set and control at 180°C to form ΔT=T in the extrusion mold cavity 2 -T 1 =50°C temperature gradient field; the extruder extrudes a 1mm thick molten sheet at a speed of 300mm / min, and passes through a ΔT'=60°C established and controlled by a far-infrared heater and a high-temperature air blowing device After the temperature gradient field, it is...
Embodiment 3
[0028] Example 3: Weigh high-density polyethylene (HDPE) and polyphenylene sulfide (PPS) at a mass percentage of 70:30, and add them to the feeding device of SHJ-20B twin-screw extruder after being fully mixed by a mixing machine , the barrel temperature of the extruder is set and controlled at 130-300°C from the solid conveying section to the melt conveying section (outlet); The mold body is constructed and insulated with heat insulating material, wherein the temperature T of the upper mold body 1 Set and control at 280°C, while the temperature of the lower die body T 2 Set and control at 320°C, the ΔT=T formed in the extrusion mold cavity 2 -T 1 =40°C temperature gradient field; the extruder extrudes a 0.5mm thick molten sheet at a speed of 300mm / min, and then passes through a temperature gradient field greater than the mold cavity ΔT'=50°C, and then cools in the shaping device Shaped into a gradient functional sheet; this specific temperature gradient field is establishe...
PUM
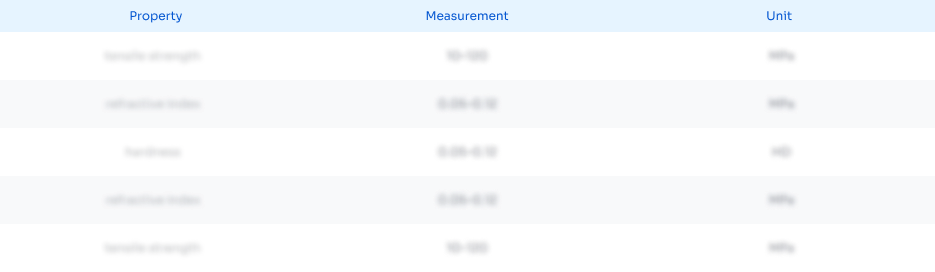
Abstract
Description
Claims
Application Information

- R&D
- Intellectual Property
- Life Sciences
- Materials
- Tech Scout
- Unparalleled Data Quality
- Higher Quality Content
- 60% Fewer Hallucinations
Browse by: Latest US Patents, China's latest patents, Technical Efficacy Thesaurus, Application Domain, Technology Topic, Popular Technical Reports.
© 2025 PatSnap. All rights reserved.Legal|Privacy policy|Modern Slavery Act Transparency Statement|Sitemap|About US| Contact US: help@patsnap.com