Robot MIG welding binocular vision sensing system
A binocular vision and sensing system technology, applied in the field of robot MIG welding binocular vision sensing system, can solve the problems of fixed shooting angle, few passive visual sensing systems, inability to flexibly adjust camera shooting angle images, etc., to reduce Unnecessary collision, reduced bearing pressure, enhanced versatility
- Summary
- Abstract
- Description
- Claims
- Application Information
AI Technical Summary
Problems solved by technology
Method used
Image
Examples
Embodiment Construction
[0023] The embodiments of the present invention are described in detail below. This embodiment is implemented on the premise of the technical solution of the present invention, and detailed implementation methods and specific operating procedures are provided, but the protection scope of the present invention is not limited to the following implementation example.
[0024] Such as figure 1 As shown, this embodiment includes: a first welding torch fixing sleeve 1, a second welding torch fixing sleeve 2, a first sensor sleeve connection block 3, a second sensor sleeve connection block 4, a molten pool observation module 5 and a welding seam Tracking module 6, wherein: molten pool observation module 5 and weld seam tracking module 6 are respectively fixed in the first welding torch fixing sleeve 1 and the second welding torch fixing sleeve 2 and are respectively connected with the first sensor sleeve connecting block 3 and the second The sensor sleeve connection blocks 4 are con...
PUM
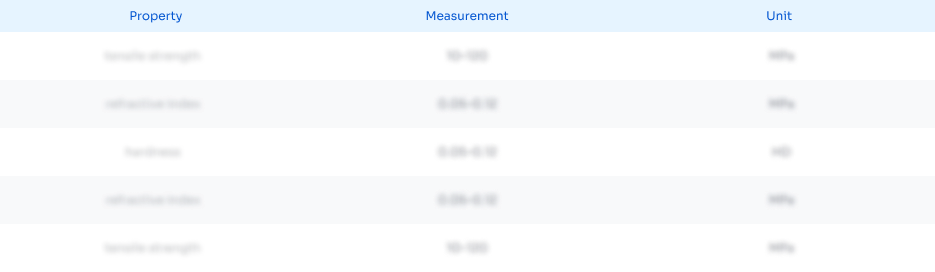
Abstract
Description
Claims
Application Information

- Generate Ideas
- Intellectual Property
- Life Sciences
- Materials
- Tech Scout
- Unparalleled Data Quality
- Higher Quality Content
- 60% Fewer Hallucinations
Browse by: Latest US Patents, China's latest patents, Technical Efficacy Thesaurus, Application Domain, Technology Topic, Popular Technical Reports.
© 2025 PatSnap. All rights reserved.Legal|Privacy policy|Modern Slavery Act Transparency Statement|Sitemap|About US| Contact US: help@patsnap.com