Preparation technology of forging elbow
A preparation process and elbow technology, which is applied in the field of forged elbow preparation process, can solve problems such as cracking at thin wall parts, affecting product service life, uneven wall thickness of inner and outer rings of elbows, etc., and achieves the effect of simple process
- Summary
- Abstract
- Description
- Claims
- Application Information
AI Technical Summary
Problems solved by technology
Method used
Image
Examples
Embodiment Construction
[0009] The present invention will be further described below in conjunction with the accompanying drawings.
[0010] Forged tube: fix the forged rod and punch it into a forged tube. The eccentricity of the forged tube is 4% to 6% of the wall thickness of the finished elbow;
[0011] Bending: according to the material of the forged pipe, heat the forged pipe to 1050-1200°C after heat treatment, and then sandblast and grind the inner and outer surfaces of the forged pipe as required, and remove the wall of the forged pipe formed by the eccentricity. The thin part of the semicircular pipe wall is used as the inner ring of the elbow, and the thick semicircular pipe wall is used as the outer ring of the elbow, and the forged pipe is bent into an elbow, so that the bent wall of the elbow is The thickness is relatively uniform, so that the elbow with uniform wall thickness can be obtained after a little finishing treatment such as grinding. In addition, the bent elbow can be subjecte...
PUM
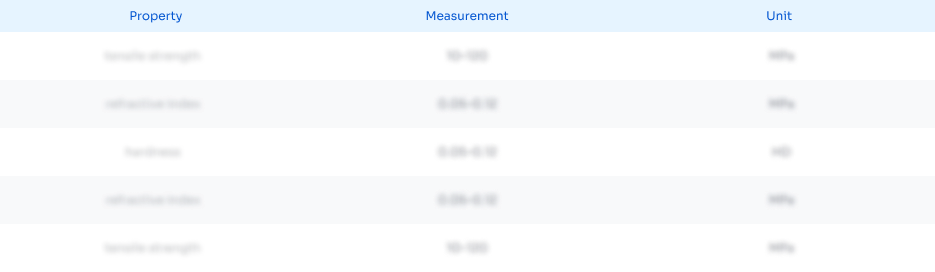
Abstract
Description
Claims
Application Information

- R&D
- Intellectual Property
- Life Sciences
- Materials
- Tech Scout
- Unparalleled Data Quality
- Higher Quality Content
- 60% Fewer Hallucinations
Browse by: Latest US Patents, China's latest patents, Technical Efficacy Thesaurus, Application Domain, Technology Topic, Popular Technical Reports.
© 2025 PatSnap. All rights reserved.Legal|Privacy policy|Modern Slavery Act Transparency Statement|Sitemap|About US| Contact US: help@patsnap.com