Non-vacuum semi-solid stirring brazing method for aluminum alloy and composite material thereof
A technology of composite materials and brazing methods, applied in welding equipment, metal processing equipment, manufacturing tools, etc., can solve the problems of semi-solid connection technology that have not been reported, and achieve the effects of overcoming adverse consequences, reliable joints, and improving performance
- Summary
- Abstract
- Description
- Claims
- Application Information
AI Technical Summary
Problems solved by technology
Method used
Image
Examples
Embodiment 1
[0034]Embodiment 1: The aluminum-based composite material weldment 1 is installed and clamped on the welding platform 4 and Zn-Al medium-temperature solder 2 is placed on the two surfaces to be welded. The solder 2 can be in the form of a sheet, a square column, a coating or sprayed on it in advance. surface to be welded. The weldment is heated by the resistance heater 3, and the heating temperature is between 390-420° C., such as 390° C., 400° C., 410° C., 420° C., so that the solder 2 is partially melted. Then start the rotary slide device, the track type sliding platform 7 drives the stirring head 5 to move, and the rotating motor 8 installed on the motor support 9 drives its rotation, and the rotational speed is 150-300 rev / min, such as 150 rev / min, 180 rev / min. rev / min, 200 rev / min, 230 rev / min, 250 rev / min, 280 rev / min or 300 rev / min, the temperature is constant during the rotation, the longitudinal moving speed of the stirring head 5 parallel to the weld seam is 0.5 -2...
Embodiment 2
[0035] Example 2, the second embodiment of the present invention is based on the first embodiment, after one rotation, the holding temperature is between 430-440°C, such as 430°C, 435°C, 440°C, and the holding time In 2-5 minutes, the solder 2 in the middle is further melted. Subsequently, start the rotating slide device again (secondary rotation), the rotation speed is 100-150 rpm, such as 100 rpm, 120 rpm, 150 rpm, the stirring head slides in the opposite direction, and the moving speed is 1-1.5 cm / min. When the stirring head moves to the initial end of the weld, stop the rotation, lift the stirring head, keep warm for 15-30 minutes, such as 15 minutes, 22 minutes, 27 minutes, 30 minutes, and cool with the furnace.
PUM
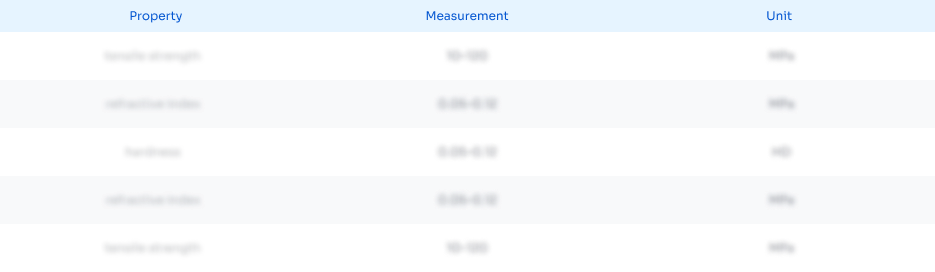
Abstract
Description
Claims
Application Information

- R&D
- Intellectual Property
- Life Sciences
- Materials
- Tech Scout
- Unparalleled Data Quality
- Higher Quality Content
- 60% Fewer Hallucinations
Browse by: Latest US Patents, China's latest patents, Technical Efficacy Thesaurus, Application Domain, Technology Topic, Popular Technical Reports.
© 2025 PatSnap. All rights reserved.Legal|Privacy policy|Modern Slavery Act Transparency Statement|Sitemap|About US| Contact US: help@patsnap.com