Cold belt rolling mill panel thickness control limited frequency domain feedforward compensation method based on wave function
A feedforward compensation, wave function technology, applied in the direction of rolling force/roll gap control, etc., can solve the problem of servo follow response time uncertainty, weakening feedforward compensation, laser speed measurement interference and other problems
- Summary
- Abstract
- Description
- Claims
- Application Information
AI Technical Summary
Problems solved by technology
Method used
Image
Examples
Embodiment
[0088] Figure 6 It is an embodiment disclosed by the present invention. The plate thickness control system adopts a typical method of adding thickness to the inner ring of the position. The initial setting value of the position ring is calculated according to the setting model, and the displacement of the oil cylinder is adjusted to the set value through the position closed loop Value. The entrance thickness is measured by the entrance thickness gauge, and the entrance strip speed is measured by the speed measuring roller encoder and converted into line speed. The strip thickness wave function description in the rolling process is constructed by the entrance thickness and the entrance strip speed, and then through the finite frequency The feed-forward controller obtains the position correction value and sends it to the position loop to achieve the purpose of feed-forward compensation for the entrance thickness. The outlet thickness is measured by the outlet thickness gauge, ...
PUM
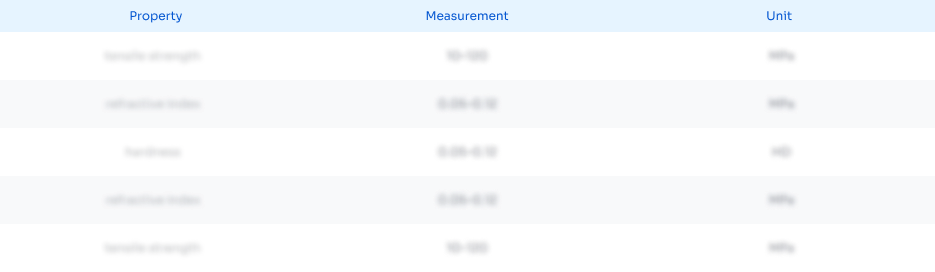
Abstract
Description
Claims
Application Information

- R&D
- Intellectual Property
- Life Sciences
- Materials
- Tech Scout
- Unparalleled Data Quality
- Higher Quality Content
- 60% Fewer Hallucinations
Browse by: Latest US Patents, China's latest patents, Technical Efficacy Thesaurus, Application Domain, Technology Topic, Popular Technical Reports.
© 2025 PatSnap. All rights reserved.Legal|Privacy policy|Modern Slavery Act Transparency Statement|Sitemap|About US| Contact US: help@patsnap.com