High strength silicon nitride combined silicon carbide material and method for preparing same
A technology of silicon nitride and silicon carbide, which is applied in the field of high-strength silicon nitride combined with silicon carbide materials and its preparation, can solve the problems of short life, insufficient physical and chemical properties, etc., and achieve the effect of improving product performance and promoting sintering
- Summary
- Abstract
- Description
- Claims
- Application Information
AI Technical Summary
Problems solved by technology
Method used
Examples
Embodiment Construction
[0008] Take the following weight percent raw materials:
[0009] SiC 82.3%
[0010] Si 14.7%
[0011] La 2 o 3 +Y 2 o 3 Mixture of 0.2%
[0012] Calcium Lignosulfonate Slurry 2.8%
[0013] Mixing: Put the above raw materials into a planetary mixer, the mixing temperature is 20°C, and the mixing time is 30 minutes.
[0014] Green molding: Vibration press is used, and the molding time is 15s.
[0015] Drying: put the green body above into a resistance furnace, and dry it at 110°C for 24 hours to obtain a green body.
[0016] Firing: Put the biscuit into a resistance furnace, and fire it at 1400°C for 10 hours in a nitrogen atmosphere to obtain a high-strength silicon nitride bonded silicon carbide material with the following properties:
[0017] SiC 72.17%
[0018] Si 3 N 4 21.94%
[0019] Fe 2 o 3 0.40%
[0020] Apparent porosity 13%
[0021] Bulk density 2.78g / cm 3
[0022] Normal temperature compressive strength 286MPa ...
PUM
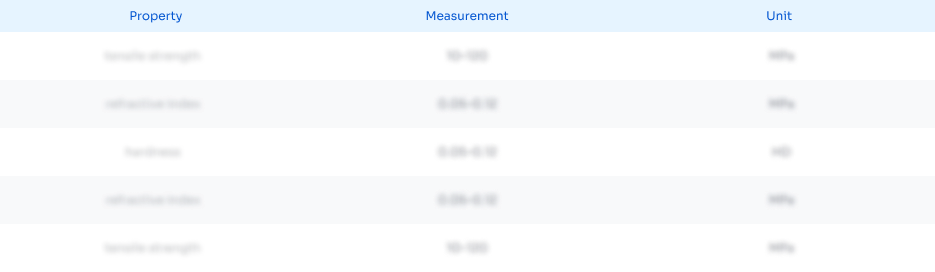
Abstract
Description
Claims
Application Information

- R&D
- Intellectual Property
- Life Sciences
- Materials
- Tech Scout
- Unparalleled Data Quality
- Higher Quality Content
- 60% Fewer Hallucinations
Browse by: Latest US Patents, China's latest patents, Technical Efficacy Thesaurus, Application Domain, Technology Topic, Popular Technical Reports.
© 2025 PatSnap. All rights reserved.Legal|Privacy policy|Modern Slavery Act Transparency Statement|Sitemap|About US| Contact US: help@patsnap.com