Scalization harvesting method and device for microalgae producing biological diesel oil
The technology of a harvesting method and harvesting device is applied in the field of large-scale harvesting method and device of biodiesel microalgae, which can solve the problems of low efficiency and high cost, and achieve the effects of simple reaction operation process, low production cost and little environmental pollution
- Summary
- Abstract
- Description
- Claims
- Application Information
AI Technical Summary
Problems solved by technology
Method used
Image
Examples
Embodiment 1
[0032] Add 5L of Chlorella to be harvested (the culture period is 10 days, and the initial optical density (OD) value is about 1.5) into the liquid separator, and 5mL of 15mol / L NaOH solution is added to the separator from the alkali storage solution tank. , and reacted for 1 h at normal temperature and pressure (stir for 5 min, then stand for 55 min), and the OD value of the supernatant was measured to be 0.052. After the reaction, the algae settle to the bottom of the liquid separation device, open the control valve at the bottom of the liquid separation device, and release the algae for oil extraction and biodiesel preparation, and the supernatant of the liquid separation is recovered for the cultivation of microalgae. The collected algal liquid and supernatant were sampled for analysis, and the results are shown in Table 1.
Embodiment 2
[0034] Add 5L of Chlorella to be harvested (the culture period is 10 days, and the initial optical density (OD) value is about 1.5) into the liquid separator, and add 1.5mol / L of NaOH solution from the alkali storage solution tank to the liquid separator. 50mL was reacted at normal temperature and pressure for 1h (stir for 3min, then stand for 57min), and the OD value of the supernatant was measured to be 0.083. After the reaction, the algae settle to the bottom of the liquid separation device, open the control valve at the bottom of the liquid separation device, and release the algae for oil extraction and biodiesel preparation, and the supernatant of the liquid separation is recovered for the cultivation of microalgae. The collected algal liquid and supernatant were sampled for analysis, and the results are shown in Table 1.
Embodiment 3
[0036] Add 5L of Chlorella to be harvested (the culture period is 10 days, and the initial optical density (OD) value is about 1.5) into the liquid separator, and add 0.15mol / L of NaOH solution from the alkali storage solution tank to the liquid separator. 500mL was reacted under normal temperature and pressure for 1h (stir for 10min, then stand for 50min), and the OD value of the supernatant was measured to be 0.036. After the reaction, the algae settle to the bottom of the liquid separation device, open the control valve at the bottom of the liquid separation device, and release the algae for oil extraction and biodiesel preparation, and the supernatant of the liquid separation is recovered for the cultivation of microalgae. The collected algal liquid and supernatant were sampled for analysis, and the results are shown in Table 1.
PUM
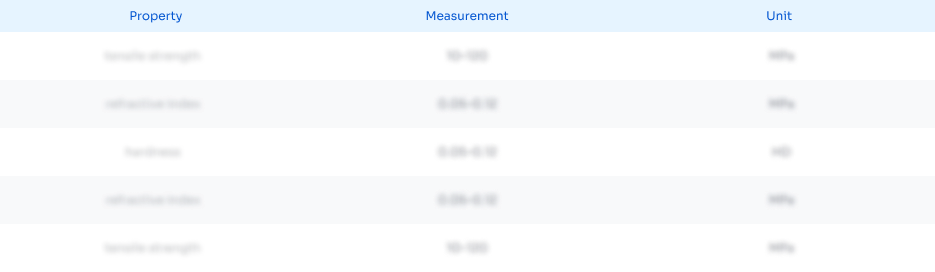
Abstract
Description
Claims
Application Information

- R&D
- Intellectual Property
- Life Sciences
- Materials
- Tech Scout
- Unparalleled Data Quality
- Higher Quality Content
- 60% Fewer Hallucinations
Browse by: Latest US Patents, China's latest patents, Technical Efficacy Thesaurus, Application Domain, Technology Topic, Popular Technical Reports.
© 2025 PatSnap. All rights reserved.Legal|Privacy policy|Modern Slavery Act Transparency Statement|Sitemap|About US| Contact US: help@patsnap.com