Surfacing compound furnace roller
A furnace roll and surfacing layer technology, which is applied in the field of equipment in the steel rolling heating furnace, can solve the problems of increasing the production cost of steel mills, not meeting the requirements of reuse, recycling, and remanufacturing, and achieves improved service life, simple temperature, and reduced The effect of production costs
- Summary
- Abstract
- Description
- Claims
- Application Information
AI Technical Summary
Problems solved by technology
Method used
Image
Examples
Embodiment Construction
[0014] from figure 1 It can be seen from the figure that a surfacing composite furnace roll includes a roll shaft 1 and a roll body 2, and the roll body is fixed on the roll shaft 1 through shoulders 3 at both ends, and the roll shaft 1 and the roll body A thermal insulation layer 4 is arranged between the body 2, air holes 5 are arranged on the body 2, and a welding layer 6 is arranged on the body 2.
[0015] In the production process, the welding material is selected according to the use requirements of the furnace roll product, and the welding material is surfacing on the roller body 2 according to the process specification. During the surfacing welding process, it is melted with the roller body 2 twice to form a finer crystal structure than the cast body. 1. The surfacing layer 6 with a denser structure, the combination of the surfacing layer 6 and the roll body 2 is a metallurgical bonding structure.
[0016] The weight percent of each component of the surfacing layer is...
PUM
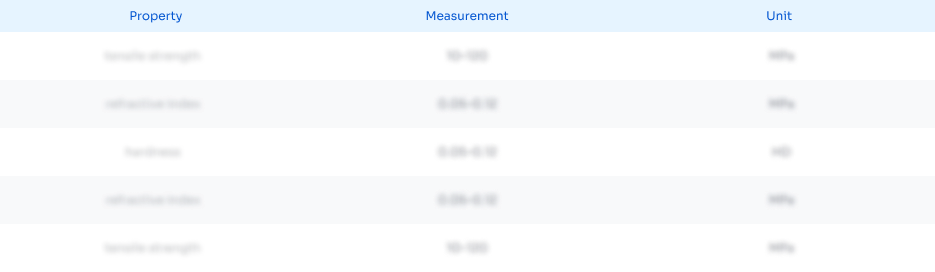
Abstract
Description
Claims
Application Information

- Generate Ideas
- Intellectual Property
- Life Sciences
- Materials
- Tech Scout
- Unparalleled Data Quality
- Higher Quality Content
- 60% Fewer Hallucinations
Browse by: Latest US Patents, China's latest patents, Technical Efficacy Thesaurus, Application Domain, Technology Topic, Popular Technical Reports.
© 2025 PatSnap. All rights reserved.Legal|Privacy policy|Modern Slavery Act Transparency Statement|Sitemap|About US| Contact US: help@patsnap.com