Hard surfacing sintered flux and manufacturing method thereof
A technology of sintering flux and manufacturing method, which is applied in the direction of manufacturing tools, welding media, welding equipment, etc., can solve the adverse effects of high-temperature slag removal of flux, adjust the hardness of surfacing metal, and easily induce surfacing cracks, etc., to achieve surfacing Excellent workmanship, high temperature oxidation corrosion resistance and improved cold and heat fatigue resistance, and excellent performance
- Summary
- Abstract
- Description
- Claims
- Application Information
AI Technical Summary
Problems solved by technology
Method used
Examples
Embodiment Construction
[0020] According to the content of the components designed in the present invention, four kinds of flux powders are prepared, and the formula numbers are F1-F4. The four formula fluxes F1 to F4 all adopt the same manufacturing process, that is, use sodium silicate glass as the binder, which accounts for 20% of the total weight of the dry powder of the sintered flux for hard surface surfacing, and first go through dry mixing, wet mixing, and granulation, and then Dry at 230°C for 25 minutes at low temperature, then sinter at 720°C for 40 minutes, and hold at 380°C for 1.5 hours before surfacing. F1~F4 fluxes of four formulas are all matched with Φ4.0mm 2Cr13 welding wire, and the surfacing welding is carried out on the 20mm thick carbon steel plate. The welding specifications are shown in Table 1. The surfacing welded metal is processed into a hardness sample on a planer, that is, a platform with a length of not less than 70 mm and a width of not less than 15 mm parallel to the...
PUM
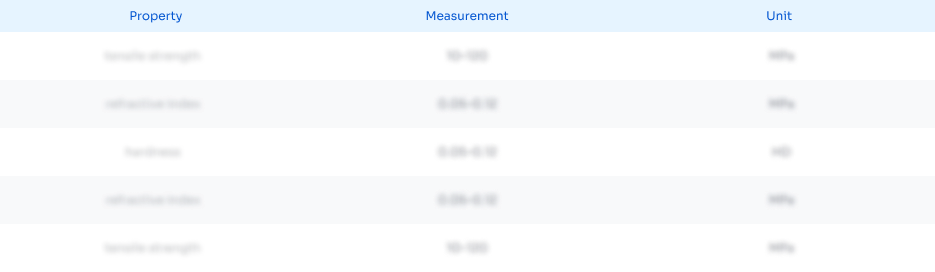
Abstract
Description
Claims
Application Information

- R&D
- Intellectual Property
- Life Sciences
- Materials
- Tech Scout
- Unparalleled Data Quality
- Higher Quality Content
- 60% Fewer Hallucinations
Browse by: Latest US Patents, China's latest patents, Technical Efficacy Thesaurus, Application Domain, Technology Topic, Popular Technical Reports.
© 2025 PatSnap. All rights reserved.Legal|Privacy policy|Modern Slavery Act Transparency Statement|Sitemap|About US| Contact US: help@patsnap.com