Annealing method for improving luminous efficiency of cerium-doped yttrium aluminum garnet crystal
A yttrium aluminum garnet, crystal luminescence technology, applied in crystal growth, chemical instruments and methods, single crystal growth and other directions, can solve problems such as affecting the luminous efficiency of crystals, and achieve improved scintillation performance, transmission performance, and luminous intensity. Effect
- Summary
- Abstract
- Description
- Claims
- Application Information
AI Technical Summary
Problems solved by technology
Method used
Image
Examples
Embodiment 1
[0029] The Ce:YAG crystal was air annealed at 1100℃.
[0030] Annealing process steps:
[0031] (1) Clean with alcohol first, the size is 20×15×2mm 3 The Ce:YAG crystal removes impurities on the surface of the crystal to avoid furnace pollution caused by volatilization of impurities.
[0032] (2) Put the Ce:YAG sample on the pure YAG crystal substrate, and put the sample up to increase the contact area with the annealing atmosphere.
[0033] (3) Start the heating program, and raise the temperature from room temperature to 1000° C. at a rate of 100° C. / hour, and then increase the temperature from 1000° C. to 1100° C. at a rate of 50° C. / hour.
[0034] (4) Constant temperature at 1100° C. for 20 hours.
[0035] (5) Cool down from 1100°C to 1000°C at a rate of 50°C / hour, and then from 1000°C to room temperature at a rate of 100°C / hour. The Ce:YAG crystal sample taken out at last is intact and not cracked.
Embodiment 2
[0037] The Ce:YAG crystal was air annealed at 1100℃.
[0038] Annealing process steps:
[0039] (1) Clean the Ce:YAG crystal with a size of 20×15×5 mm3 with alcohol to remove impurities existing on the surface of the crystal, so as to avoid contamination of the furnace caused by volatilization of impurities.
[0040] (2) Put the Ce:YAG sample on the pure YAG crystal substrate, and put the sample up to increase the contact area with the annealing atmosphere.
[0041] (3) Start the heating program, and raise the temperature from room temperature to 1000° C. at a rate of 100° C. / hour, and then increase the temperature from 1000° C. to 1100° C. at a rate of 50° C. / hour.
[0042] (4) Constant temperature at 1100° C. for 35 hours.
[0043](5) Cool down from 1100°C to 1000°C at a rate of 50°C / hour, and then from 1000°C to room temperature at a rate of 100°C / hour. The Ce:YAG crystal sample taken out at last is intact and not cracked.
Embodiment 3
[0045] The Ce:YAG crystal was air annealed at 1200℃.
[0046] Annealing process steps:
[0047] (1) Clean with alcohol first, the size is 20×15×2mm 3 The Ce:YAG crystal removes impurities on the surface of the crystal to avoid furnace pollution caused by volatilization of impurities.
[0048] (2) Put the Ce:YAG sample on the pure YAG crystal substrate, and put the sample up to increase the contact area with the annealing atmosphere.
[0049] (3) Start the heating program, and raise the temperature from room temperature to 1000°C at a rate of 100°C / hour, and then increase the temperature from 1000°C to 1200°C at a rate of 50°C / hour.
[0050] (4) Constant temperature at 1200° C. for 15 hours.
[0051] (5) Cool down first from 1200°C to 1000°C at a rate of 50°C / hour, and then from 1000°C to room temperature at a rate of 100°C / hour. The Ce:YAG crystal sample taken out at last is intact and not cracked. The transmission and luminescence effects before and after annealing are a...
PUM
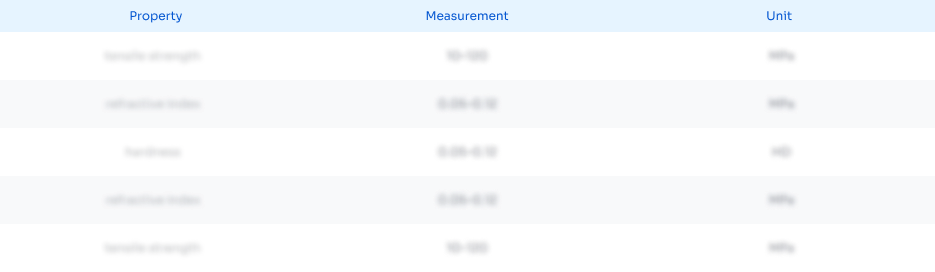
Abstract
Description
Claims
Application Information

- R&D
- Intellectual Property
- Life Sciences
- Materials
- Tech Scout
- Unparalleled Data Quality
- Higher Quality Content
- 60% Fewer Hallucinations
Browse by: Latest US Patents, China's latest patents, Technical Efficacy Thesaurus, Application Domain, Technology Topic, Popular Technical Reports.
© 2025 PatSnap. All rights reserved.Legal|Privacy policy|Modern Slavery Act Transparency Statement|Sitemap|About US| Contact US: help@patsnap.com