Process and multistage fluidized bed for hematite prereduction
A fluidized bed and fine iron ore technology, which is applied in the field of multi-stage fluidized bed devices, can solve the problems of raw material melting and bonding, and achieve the effects of preventing melting and bonding, improving recycling, and increasing process energy consumption
Active Publication Date: 2010-12-01
BAOSHAN IRON & STEEL CO LTD
View PDF2 Cites 0 Cited by
- Summary
- Abstract
- Description
- Claims
- Application Information
AI Technical Summary
Problems solved by technology
The purpose of the present invention is to develop a multi-stage fluidized bed device and process for pre-reduction of fine iron ore, to overcome the excessively high gas temperature caused by the current multi-stage fluidized bed pre-reduction fine iron ore process and the final reduction process. The problem of raw material melting and bonding, and reducing the pressure loss of the gas distribution plate in the multi-stage fluidized bed reduction fine iron ore process device, improving the efficiency of the multi-stage fluidized bed pre-reduction fine iron ore process, thereby improving the overall "two-step" melting Reduction process efficiency
Method used
the structure of the environmentally friendly knitted fabric provided by the present invention; figure 2 Flow chart of the yarn wrapping machine for environmentally friendly knitted fabrics and storage devices; image 3 Is the parameter map of the yarn covering machine
View moreImage
Smart Image Click on the blue labels to locate them in the text.
Smart ImageViewing Examples
Examples
Experimental program
Comparison scheme
Effect test
Embodiment 1
Embodiment 2
Embodiment 3
the structure of the environmentally friendly knitted fabric provided by the present invention; figure 2 Flow chart of the yarn wrapping machine for environmentally friendly knitted fabrics and storage devices; image 3 Is the parameter map of the yarn covering machine
Login to View More PUM
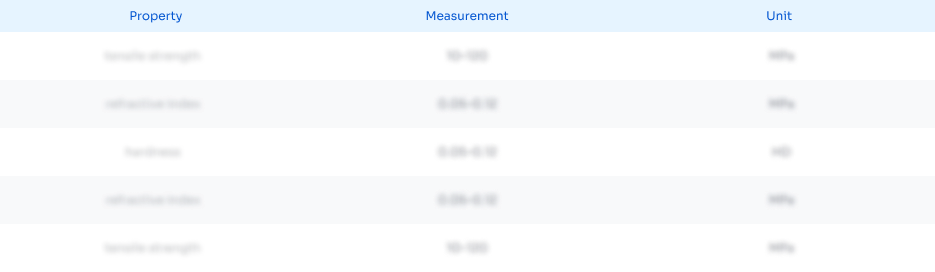
Abstract
The invention relates to a multistage fluidized bed which is used in hematite prereduction process and formed by at least two stages of fluidized beds sequentially connected in series. The raw materiaThe invention relates to a multistage fluidized bed which is used in hematite prereduction process and formed by at least two stages of fluidized beds sequentially connected in series. The raw materiaused by over-high temperature of coal gas in the existing multistage fluidized bed prereduction process, reduces the pressure loss of the gas distribution plate in the multistage fluidized bed, and iaused by over-high temperature of coal gas in the existing multistage fluidized bed prereduction process, reduces the pressure loss of the gas distribution plate in the multistage fluidized bed, and improves the working efficiency of fluidized bed hematite prereduction process, thereby improving the efficiency of smelting reduction process by the whole 'two-step method'.mproves the working efficiency of fluidized bed hematite prereduction process, thereby improving the efficiency of smelting reduction process by the whole 'two-step method'.l of hematite is put in the first stage fluidized bed from a storage bin, high temperature coal gas taken as fluidizing medium and reaction medium is led into from the bottom of the last stage of fluil of hematite is put in the first stage fluidized bed from a storage bin, high temperature coal gas taken as fluidizing medium and reaction medium is led into from the bottom of the last stage of fluidized bed; the raw material of hematite goes downstream by gravity, the high temperature coal gas goes in a reverse direction with the hematite, and the hematite is reduced step by step in the multistdized bed; the raw material of hematite goes downstream by gravity, the high temperature coal gas goes in a reverse direction with the hematite, and the hematite is reduced step by step in the multistage fluidized beds; the hematite is reduced by the multistage fluidized beds or added directly into a final reduction furnace by gravity, or sprayed into the final reduction furnace by a spraying gun;age fluidized beds; the hematite is reduced by the multistage fluidized beds or added directly into a final reduction furnace by gravity, or sprayed into the final reduction furnace by a spraying gun;and the fluidized bed is provided with at least two tapers, and is a tapered fluidized bed without a gas distribution plate. The invention solves the problem of smelting and bonding of raw material c and the fluidized bed is provided with at least two tapers, and is a tapered fluidized bed without a gas distribution plate. The invention solves the problem of smelting and bonding of raw material ca
Description
A multi-stage fluidized bed device and process for pre-reduction of fine iron ore technical field The invention relates to a smelting reduction ironmaking process in the field of ironmaking, in particular to a multistage fluidized bed device and process for pre-reduction of fine iron ore. Background technique The blast furnace ironmaking process is currently the main ironmaking process, but the overall process of the blast furnace ironmaking process is long, the pollution is serious, and the dependence on coking coal is the bottleneck that the process itself cannot break through. The smelting reduction ironmaking process is expected to overcome the limitations of the blast furnace ironmaking process , in the case of increasingly scarce resources and increasing pressure on environmental protection, the smelting reduction ironmaking process has increasingly highlighted its importance. Among the many developed smelting reduction ironmaking processes, the "two-step" smelting r...
Claims
the structure of the environmentally friendly knitted fabric provided by the present invention; figure 2 Flow chart of the yarn wrapping machine for environmentally friendly knitted fabrics and storage devices; image 3 Is the parameter map of the yarn covering machine
Login to View More Application Information
Patent Timeline

Patent Type & Authority Patents(China)
IPC IPC(8): C21B13/14
Inventor 范建峰李维国周渝生李肇毅张友平
Owner BAOSHAN IRON & STEEL CO LTD
Who we serve
- R&D Engineer
- R&D Manager
- IP Professional
Why Patsnap Eureka
- Industry Leading Data Capabilities
- Powerful AI technology
- Patent DNA Extraction
Social media
Patsnap Eureka Blog
Learn More Browse by: Latest US Patents, China's latest patents, Technical Efficacy Thesaurus, Application Domain, Technology Topic, Popular Technical Reports.
© 2024 PatSnap. All rights reserved.Legal|Privacy policy|Modern Slavery Act Transparency Statement|Sitemap|About US| Contact US: help@patsnap.com