Process for hydrofining coking crude benzene
A technology for hydrorefining and coking crude benzene is applied in the field of coking crude benzene hydrorefining technology, which can solve the problems of large loss of aromatic compounds and reduce the retention rate of aromatic hydrocarbons, so as to improve the retention rate, reduce the loss of aromatic compounds, and prolong the processing time. The effect of the hydrogen reaction process
- Summary
- Abstract
- Description
- Claims
- Application Information
AI Technical Summary
Problems solved by technology
Method used
Image
Examples
Embodiment 1
[0035] Embodiment 1: Raw material coking crude benzene is the coking crude benzene produced by Benxi Iron and Steel Coking Plant, and its properties are shown in the following table:
[0036] Composition of coking crude benzene data Total sulfur, ppm 6775.01 Total nitrogen, ppm 905.2 Acidity, mgKOH / 100ml 1.08 Colloid, mg / 100ml 97.4 Density, 20℃, g / ml 0.8889
[0037] The reaction part adopts three-stage hydrogenation reaction, the first-stage hydrogenation reaction is the pre-hydrogenation reaction, and the second and third-stage hydrogenation reactions are the main hydrogenation reaction. The catalyst for the second-stage hydrogenation reaction is NiMo catalyst, and the process conditions are reaction temperature 290°C, reaction pressure 2.6MPa, and volumetric space velocity 3.5h -1 , The volume ratio of hydrogen to oil is 500:1. The catalyst for the three-stage hydrogenation reaction is a CoMo catalyst, and the process conditions ...
Embodiment 2
[0042] The raw material of coking crude benzene is the same as in Example 1. The reaction part adopts three-stage hydrogenation reaction, the first-stage hydrogenation reaction is the pre-hydrogenation reaction, and the second and third-stage hydrogenation reactions are the main hydrogenation reaction. The catalyst for the second-stage hydrogenation reaction is a NiMo catalyst, and the process conditions are reaction temperature 285°C, reaction pressure 2.6MPa, volume space velocity 4.0h -1 , The volume ratio of hydrogen to oil is 500:1. The catalyst for the three-stage hydrogenation reaction is a CoMo catalyst, and the process conditions are reaction temperature 260°C, reaction pressure 2.6MPa, volume space velocity 5h -1 , The volume ratio of hydrogen to oil is 500:1. The properties of the product after hydrofining are as follows:
[0043] Second stage hydrogenation product Three-stage hydrogenation product Total sulfur, ppm 350 0.9 Total nitroge...
PUM
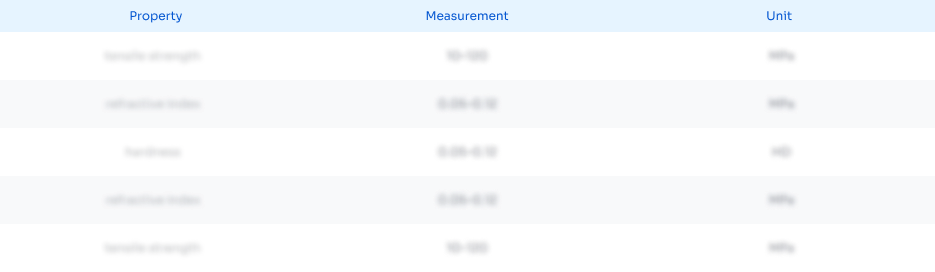
Abstract
Description
Claims
Application Information

- R&D
- Intellectual Property
- Life Sciences
- Materials
- Tech Scout
- Unparalleled Data Quality
- Higher Quality Content
- 60% Fewer Hallucinations
Browse by: Latest US Patents, China's latest patents, Technical Efficacy Thesaurus, Application Domain, Technology Topic, Popular Technical Reports.
© 2025 PatSnap. All rights reserved.Legal|Privacy policy|Modern Slavery Act Transparency Statement|Sitemap|About US| Contact US: help@patsnap.com