Numerical control gear shaping error compensation and gear profile modification method
A processing error and error compensation technology, applied in the field of CNC gear shaping, can solve the problems that the system cannot perform compensation, does not have the ability to adjust the instantaneous transmission ratio, and cannot use standard tool tooth profile modification processing, etc., and achieves easy operation and precision cost. Low, the effect of maintaining machining accuracy
- Summary
- Abstract
- Description
- Claims
- Application Information
AI Technical Summary
Problems solved by technology
Method used
Image
Examples
Embodiment 1
[0044] Embodiment 1: gear shape modification.
[0045] Number of gear teeth z 1 =16, number of gear teeth to be machined z 2 =28, modulus m n =6, pressure angle α=20°, addendum height coefficient h of gear shaper cutter a =1.3, there are three sets of modification curves in total, which are circular arc, straight line and parabola, and the modification amount Δ max =40μm, modification length h max = 4 mm. Take 15 model value points in the arc modification part of the processed gear, and solve the motion according to the principle of digital conjugate surface, and obtain the discrete points of the processed gear, the conjugate points on the gear shaper cutter, and the motion parameters. Use the calculated motion parameters to compile NC machining codes, output the codes, and perform NC machining. The measurement shows that the processing result meets the accuracy requirement of the modification curve.
[0046] Error Analysis of Arc Modification Unit μm
[0047] ...
Embodiment 2
[0048] Embodiment 2: Tooth profile error compensation.
[0049]The processing is carried out on the YKS5132 three-axis CNC gear shaping machine, and the measurement is carried out on the SP-60 involute tooth profile measuring instrument. The parameters of the processed gear are: number of teeth z=28, modulus m=8, pressure angle α=20°, addendum height coefficient h a = 1.0. Firstly, the standard CNC machining program is used for trial cutting, and the tooth profile of the gear to be cut is measured with an involute tooth profile measuring instrument. Points are collected from the measured tooth profile error curve to obtain the tooth profile error of a series of points on the tooth profile, and a new digital virtual tooth profile after error pre-compensation is constructed. Based on this virtual tooth profile, the conjugate motion is solved, and the NC code is compiled for compensation processing. The measurement shows that the machining accuracy has been improved from 8 gra...
Embodiment 3
[0050] Embodiment 3: Compensation for tooth pitch accumulative error.
[0051] Gear parameters: m=8, z=28, α=20°, processed on a YKS5132 CNC gear shaping machine. Using the error compensation system can increase the pitch error and cumulative error of the processed gear from 7 levels before compensation to 5~6 levels after compensation, improve the accuracy by more than 1 level, and the compensation effect is obvious.
[0052] Such as image 3 In, uncompensated cumulative data, suprasegmental deviation = 18.0 μm, subsegmental deviation = -11.3 μm, accumulation = 34.3 μm. Such as Figure 4 Among them, the accumulated data after compensation, the above-segment deviation = 16.2 μm, the below-segment deviation = -10.6 μm, and the accumulation = 16.3 μm.
PUM
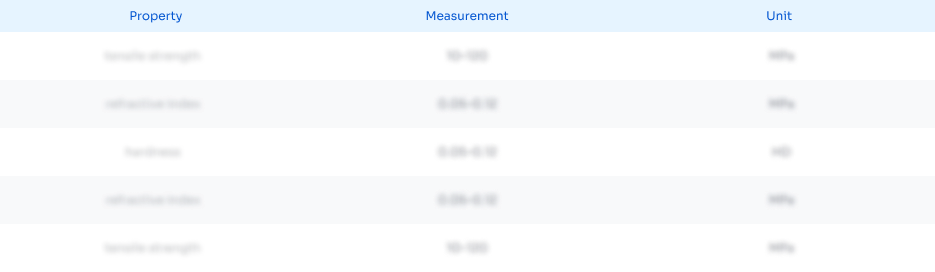
Abstract
Description
Claims
Application Information

- Generate Ideas
- Intellectual Property
- Life Sciences
- Materials
- Tech Scout
- Unparalleled Data Quality
- Higher Quality Content
- 60% Fewer Hallucinations
Browse by: Latest US Patents, China's latest patents, Technical Efficacy Thesaurus, Application Domain, Technology Topic, Popular Technical Reports.
© 2025 PatSnap. All rights reserved.Legal|Privacy policy|Modern Slavery Act Transparency Statement|Sitemap|About US| Contact US: help@patsnap.com