Method for removing trace sulfur in styrene by catalytic rectification
A technology of catalytic rectification and catalytic rectification column is applied in the field of catalytic rectification to remove trace amount of sulfur in styrene, which can solve problems such as difficulty in removal, and achieve the effect of good technical effect.
- Summary
- Abstract
- Description
- Claims
- Application Information
AI Technical Summary
Problems solved by technology
Method used
Image
Examples
Embodiment 1
[0014] The number of theoretical plates in the rectification section of the catalytic rectification tower is 10, the number of theoretical plates in the stripping section is 10, the height of the reaction section is equivalent to the height of 5 theoretical plates, the catalyst is D001 macroporous ion exchange resin, and the ion exchange resin ions The form is hydrogen ion, sulfur-containing styrene and isobutylene respectively enter from the fifth theoretical plate (counting from top to bottom, the same below) and the tower kettle of the stripping section of the catalytic rectification tower, and the flow rate of sulfur-containing styrene is 30 grams / min, the sulfur content is 150ppm, the flow rate of isobutene is 5 milliliters / min, and the reflux ratio is 6, and the output of the liquid phase at the top of the tower is 27 g / min, and the operating pressure is 4KPa. After stable operation, the desulfurization styrene at the top of the tower is The sulfur content is 10ppm, the ...
Embodiment 2
[0016] The number of theoretical plates in the rectification section of the catalytic rectification tower is 30, the number of theoretical plates in the stripping section is 30, the height of the reaction section is equivalent to the height of 20 theoretical plates, the catalyst is ZSM-5 molecular sieve catalyst, and the silicon-aluminum ratio is 45 , sulfur-containing styrene and isobutylene enter respectively from the 10th theoretical plate (counting from top to bottom, the same below) and the tower kettle of the stripping section of the catalytic rectification tower, the sulfur-containing styrene flow rate is 30 g / min, and the sulfur content is 200ppm, the flow rate of isobutylene is 135 ml / min, the reflux ratio is 0.3, the output of liquid phase at the top of the tower is 28.5 g / min, and the operating pressure is 20KPa. After the operation is stable, the sulfur content of desulfurized styrene at the top of the tower is 4ppm, and the gas phase The unreacted isobutene is extr...
Embodiment 3
[0018] The number of theoretical plates in the rectification section of the catalytic rectification tower is 15, the number of theoretical plates in the stripping section is 20, the height of the reaction section is equivalent to the height of 10 theoretical plates, the catalyst is ZSM-5 molecular sieve catalyst, and the silicon-aluminum ratio is 45 , sulfur-containing styrene and isobutylene enter respectively from the 10th theoretical plate (counting from top to bottom, the same below) and the tower kettle of the stripping section of the catalytic rectification tower, the sulfur-containing styrene flow rate is 30 g / min, and the sulfur content is 180ppm, the flow rate of isobutylene is 45 ml / min, the reflux ratio is 1.2, the output of the liquid phase at the top of the tower is 28.5 g / min, and the operating pressure is 10KPa. After the operation is stable, the sulfur content of the desulfurized styrene at the top of the tower is 8ppm, and the gas phase The unreacted isobutene ...
PUM
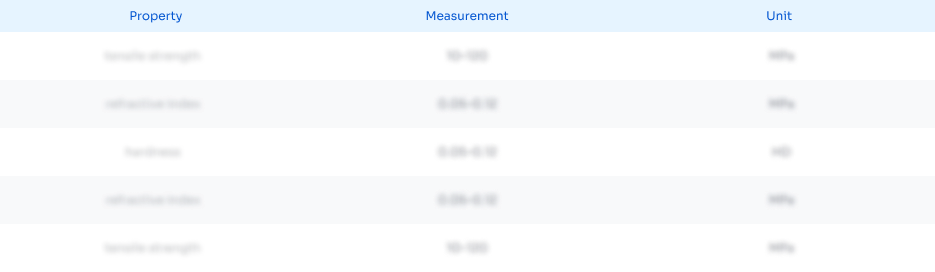
Abstract
Description
Claims
Application Information

- Generate Ideas
- Intellectual Property
- Life Sciences
- Materials
- Tech Scout
- Unparalleled Data Quality
- Higher Quality Content
- 60% Fewer Hallucinations
Browse by: Latest US Patents, China's latest patents, Technical Efficacy Thesaurus, Application Domain, Technology Topic, Popular Technical Reports.
© 2025 PatSnap. All rights reserved.Legal|Privacy policy|Modern Slavery Act Transparency Statement|Sitemap|About US| Contact US: help@patsnap.com