Three freedom degree plane motor servo controller based on dual-DSP
A technology of servo controller and planar motor, applied in the field of servo controller, can solve problems such as being susceptible to environmental interference, expensive, difficult to determine analog circuit parameters, etc., and achieve the effect of reducing costs
- Summary
- Abstract
- Description
- Claims
- Application Information
AI Technical Summary
Problems solved by technology
Method used
Image
Examples
Embodiment Construction
[0036] The present invention will be described in detail below in conjunction with the accompanying drawings.
[0037] see figure 1 , a dual-DSP-based 3-DOF planar motor servo controller is characterized in that it includes a master control unit 1 and a slave control unit 2 .
[0038] see figure 2 , the main control unit 1 includes a main DSP11, a main buffer drive module 12, a twelve-way main optocoupler isolation drive module 13, a six-phase main full-bridge power drive module 14, and a six-phase plane for sampling the output of the main control unit The main Hall current sensor module 15 of the motor drive current and the No. 1 X-axis laser position sensor 16 and the No. 2 X-axis laser position sensor 17 for sampling the X-axis positions of the first and second planar motors. The main DSP11 includes the main The ADC module on the DSP chip, the PWM module on the main DSP chip and the CAN module on the main DSP chip; the PWM signal output end of the PWM module on the main...
PUM
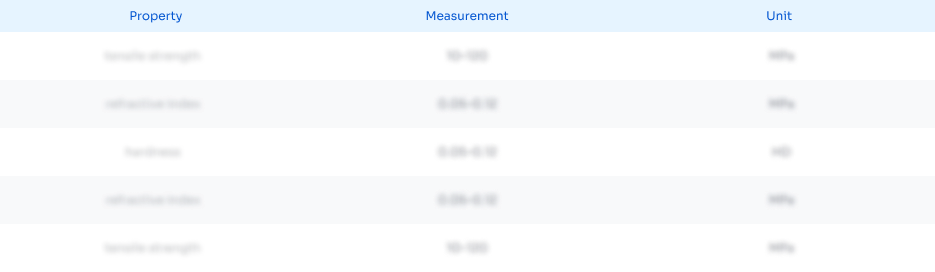
Abstract
Description
Claims
Application Information

- Generate Ideas
- Intellectual Property
- Life Sciences
- Materials
- Tech Scout
- Unparalleled Data Quality
- Higher Quality Content
- 60% Fewer Hallucinations
Browse by: Latest US Patents, China's latest patents, Technical Efficacy Thesaurus, Application Domain, Technology Topic, Popular Technical Reports.
© 2025 PatSnap. All rights reserved.Legal|Privacy policy|Modern Slavery Act Transparency Statement|Sitemap|About US| Contact US: help@patsnap.com