Methanation reaction process using oven gas to prepare substitute natural gas
A technology for synthesizing natural gas and methanation reactors, which is applied in the petroleum industry, gas fuels, fuels, etc., can solve problems such as unfavorable methanation reactions, and achieve the effects of reducing energy consumption, reducing product gas volume, and reducing costs
- Summary
- Abstract
- Description
- Claims
- Application Information
AI Technical Summary
Problems solved by technology
Method used
Image
Examples
Embodiment 1
[0035] In this example, the methanation process for producing synthetic natural gas from coke oven gas is as follows: figure 1 Shown:
[0036] First, the coke oven gas is purified to remove benzene and naphthalene, hydrogenate, and remove oxygen and desulfurization. The composition of the purified coke oven gas (vol%, dry basis, the same below) is H 2 57.6, CH 4 26.9, CO 7.2, CO 2 2.1,N 2 4.1, CnHm 2.1. The purified raw gas volume is 1000kmol / h (22400Nm 3 / h), as the raw coke oven gas for the following methanation reaction.
[0037] then follow figure 1 As shown in the process flow, a 2-stage methanation reaction is carried out using a 2-stage methanation reactor:
[0038] The raw coke oven gas is divided into two parts (400kmol and 600kmol respectively) and enters the first-stage and second-stage methanation reactors respectively:
[0039] 400kmol of raw coke oven gas 0 enters pipeline 1 at a temperature of 120°C and a pressure of 1.25MPa, and is mixed with 800km...
Embodiment 2
[0044] In this example, the methanation process for producing synthetic natural gas from coke oven gas is as follows: figure 2 Shown:
[0045] First, the coke oven gas is purified to remove benzene and naphthalene, hydrogenate, and remove oxygen and desulfurization. The composition (vol%) of the purified coke oven gas is: H 2 57.6, CH 4 26.9, CO 7.2, CO 2 2.1,N 2 4.1, CnHm 2.1. The purified raw gas volume is 1000kmol / h (22400Nm 3 / h), as the raw coke oven gas for the following methanation reaction.
[0046] then follow figure 2 As shown in the process flow, a 3-stage methanation reaction is carried out using a 3-stage methanation reactor:
[0047] The raw material coke oven gas is divided into three parts (respectively 250kmol, 350kmol and 400kmol) into the first-stage, second-stage and third-stage methanation reactors respectively:
[0048] The first part of 250kmol raw coke oven gas 0 enters pipeline 1 at a temperature of 120°C and a pressure of 1.25MPa, and i...
Embodiment 3
[0054] In this example, the methanation process for producing synthetic natural gas from coke oven gas is as follows: image 3 Shown:
[0055] First, the coke oven gas is purified to remove benzene and naphthalene, hydrogenate, and remove oxygen and desulfurization. The composition (vol%) of the purified coke oven gas is: H 2 57.6, CH 4 26.9, CO 7.2, CO 2 2.1,N 2 4.1, CnHm 2.1. The purified raw gas volume is 1000kmol / h (22400Nm 3 / h), as the raw coke oven gas for the following methanation reaction.
[0056] then follow image 3 As shown in the process flow, a 4-stage methanation reaction is carried out using a 4-stage methanation reactor:
[0057] Raw coke oven gas is divided into four parts (respectively 150kmol, 200kmol, 300kmol and 350kmol) into the first-stage, second-stage, third-stage and fourth-stage methanation reactors:
[0058] The first part of 150kmol raw coke oven gas 0 enters pipeline 1 at a temperature of 120°C and a pressure of 1.25MPa, and is mixe...
PUM
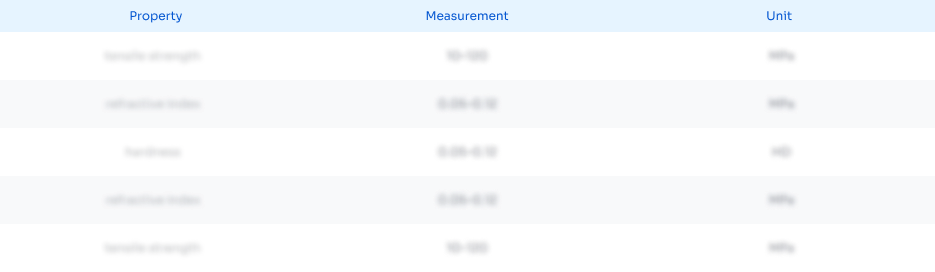
Abstract
Description
Claims
Application Information

- R&D
- Intellectual Property
- Life Sciences
- Materials
- Tech Scout
- Unparalleled Data Quality
- Higher Quality Content
- 60% Fewer Hallucinations
Browse by: Latest US Patents, China's latest patents, Technical Efficacy Thesaurus, Application Domain, Technology Topic, Popular Technical Reports.
© 2025 PatSnap. All rights reserved.Legal|Privacy policy|Modern Slavery Act Transparency Statement|Sitemap|About US| Contact US: help@patsnap.com