Spray finishing polyurethane rigid foam raw material and foam produced thereof
A technology for spraying polyurethane and rigid foam, applied in the field of polyurethane foam, can solve the problems of poor adhesion, poor adhesion between foam and substrate, high foam density, etc., and achieve good dimensional stability and good flame retardant performance. , the effect of low thermal conductivity
- Summary
- Abstract
- Description
- Claims
- Application Information
AI Technical Summary
Problems solved by technology
Method used
Image
Examples
Embodiment 1
[0019] B component:
[0020] 20-50 parts of polyester polyol
[0021] 10-40 parts of polyether polyol
[0022] Silicone oil 1.0 parts
[0023] 0.2-0.6 parts of water
[0024] Catalyst 2-8 parts
[0025] Flame retardant 10-30 parts
[0026] Foaming agent HCFC-22 2-8 parts
[0027] Foaming agent HCFC-141b 10-30 parts
[0028] A component:
[0029] Polymethylene polyphenylisocyanate PM-200 110 parts
[0030] The polyurethane rigid foam generated after construction according to the above components A and B has the following properties.
[0031]
Embodiment 2
[0033] raw material:
[0034] B component:
[0035] 20-50 parts of polyester polyol
[0036] 10-40 parts of polyether polyol
[0037] Silicone oil 1.0 parts
[0038] 0.2-0.6 parts of water
[0039] Catalyst 2-8 parts
[0040] Flame retardant 10-30 parts
[0041] Foaming agent HFC-134a 1-8 parts
[0042] Foaming agent HCFC-141b 10-30 parts
[0043] A component:
[0044] Polymethylene polyphenylisocyanate PM-200 110 parts
[0045] The polyurethane rigid foam generated after construction according to the above components A and B has the following properties.
[0046]
Embodiment 3
[0048] B component:
[0049] 20-50 parts of polyester polyol
[0050] 10-40 parts of polyether polyol
[0051] Silicone oil 1.0 parts
[0052] 0.2-0.6 parts of water
[0053] Catalyst 2-8 parts
[0054] Flame retardant 10-30 parts
[0055] Foaming agent HCFC-22 2-8 parts
[0056] Foaming agent HFC-134a 1-8 parts
[0057] Foaming agent HCFC-141b 10-30 parts
[0058] A component:
[0059] Polymethylene polyphenylisocyanate PM-200 110 parts
[0060] The polyurethane rigid foam generated after construction according to the above components A and B has the following properties.
[0061]
PUM
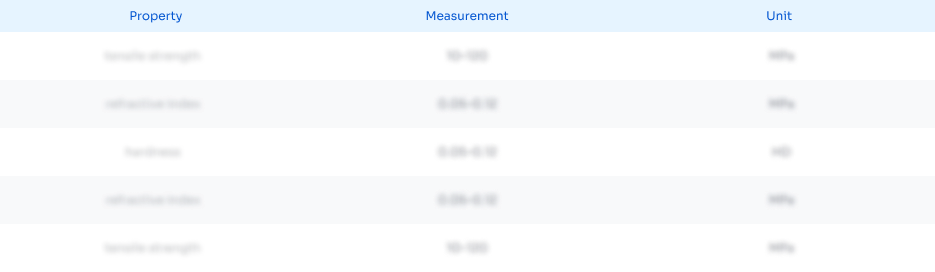
Abstract
Description
Claims
Application Information

- R&D Engineer
- R&D Manager
- IP Professional
- Industry Leading Data Capabilities
- Powerful AI technology
- Patent DNA Extraction
Browse by: Latest US Patents, China's latest patents, Technical Efficacy Thesaurus, Application Domain, Technology Topic, Popular Technical Reports.
© 2024 PatSnap. All rights reserved.Legal|Privacy policy|Modern Slavery Act Transparency Statement|Sitemap|About US| Contact US: help@patsnap.com