Dehydrogenation ammoniation method for producing pyrrolidine with 1,4butanediol
A technology of tetrahydropyrrole and butanediol, which is applied in chemical instruments and methods, metal/metal oxide/metal hydroxide catalysts, organic chemistry, etc., can solve the problem of increasing the difficulty of product purification, high equipment requirements, and unfavorable large-scale Large-scale industrial production and other issues, to achieve the effect of reducing the difficulty of product purification and separation, high conversion rate and yield of raw materials, and easy sewage treatment
- Summary
- Abstract
- Description
- Claims
- Application Information
AI Technical Summary
Problems solved by technology
Method used
Examples
Embodiment 1
[0008] Embodiment 1: use gas phase fixed bed as reactor, add 3~5mm granular SO in gas phase fixed bed 4 2- / MxOy rare earth metal compound supported catalyst (for SO 4 2- / TiO 2 -SnO 2 -Al 2 o 3 Solid superacid catalyst) 150g; heat up to 280°C at a space velocity of 50-55cm 3 / min Input nitrogen into the reactor, so that the catalyst is always under the protection of nitrogen. Use a metering pump to feed 1,4-butanediol and water in a ratio (molar ratio) of 1:0.4, and feed the vapor of 1,4-butanediol and water into the reactor at a weight space velocity of 0.6g / min. At the same time, feed ammonia gas to make the molar ratio of 1,4-butanediol and ammonia 1:1.3, and make the molar ratio of 1,4-butanediol, ammonia and water 1:1.3:0.4. The reaction pressure is 0-0.1Mpa. The above-mentioned raw materials generate a mixture under the action of a catalyst, and the objects flowing out from the outlet of the reactor are condensed by a condensing device to obtain a mixture solve...
Embodiment 2
[0009] Embodiment 2: Different from Embodiment 1 is SO 4 2- / MxOy rare earth metal compound supported catalyst is SO 4 2- / CuO-ZnO-Al 2 o 3 Solid superacid catalyst; the molar ratio of 1,4-butanediol, ammonia and water is 1:1.5:1. The reaction temperature is 290°C. The conversion rate of 1,4-butanediol is 100%, the yield rate of tetrahydropyrrole is 91%, and the by-product is mainly water. The rest is the same. So I won't repeat it any more.
Embodiment 3
[0010] Embodiment 3: Different from Embodiment 1 is SO 4 2- / MxOy rare earth metal compound supported catalyst is SO 4 2- / TiO 2 -SnO 2 -Al 2 o 3 Solid superacid catalyst; the molar ratio of 1,4-butanediol, ammonia and water is 1:2:3. The steam of 1,4-butanediol and water is fed into the reactor at a weight space velocity of 0.7 g / min. The reaction temperature is 320°C. The conversion rate of 1,4-butanediol is 100%, the yield rate of tetrahydropyrrole is 90.5%, and the by-product is mainly water. The rest is the same. So I won't repeat it any more.
[0011] SO 4 2- / TiO 2 -SnO 2 -Al 2 o 3 Solid superacid catalyst and SO 4 2- / CuO-ZnO-Al 2 o 3 The solid superacid catalysts are all existing products.
PUM
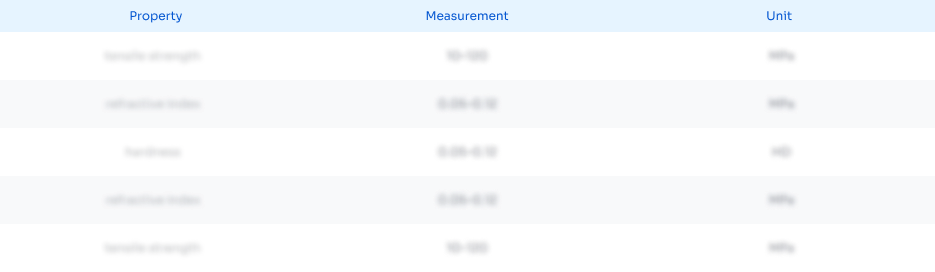
Abstract
Description
Claims
Application Information

- R&D
- Intellectual Property
- Life Sciences
- Materials
- Tech Scout
- Unparalleled Data Quality
- Higher Quality Content
- 60% Fewer Hallucinations
Browse by: Latest US Patents, China's latest patents, Technical Efficacy Thesaurus, Application Domain, Technology Topic, Popular Technical Reports.
© 2025 PatSnap. All rights reserved.Legal|Privacy policy|Modern Slavery Act Transparency Statement|Sitemap|About US| Contact US: help@patsnap.com