Method for in situ modification by isoelectric point layered composite metal hydroxides
A layered composite, hydroxide technology, applied in the preparation of oxide/hydroxide, alumina/aluminum hydroxide, etc., can solve the problems of increased production cost, large production water consumption, consumption of washing water, etc. The effect of washing water consumption, simplifying the washing process, and avoiding ion agglomeration
- Summary
- Abstract
- Description
- Claims
- Application Information
AI Technical Summary
Problems solved by technology
Method used
Image
Examples
Embodiment 1
[0031] 102.5g Mg(NO 3 )·6H 2 O and 75.0gAl(NO 3 ) 3 9H 2 O was dissolved in deionized water to form a 500ml mixed salt solution, and 38.4g NaOH and 42.3g NaOH 2 CO 3 Make 500ml alkali solution with water, add the two solutions into the total back-mixed liquid membrane reactor at the same time, place the obtained slurry in a 2L flask and heat to reflux under stirring conditions, and react for 6 hours to obtain Mg 4 al 2 (OH) 12 CO 3 4H 2 O slurry. The slurry was cooled to room temperature, and the pH value of the slurry was determined to be 10.6. The slurry was divided into 4 parts, each containing about 5g of the product, and the Mg was measured with a DXD2II type TV microelectrophoresis instrument. 4 al 2 (OH) 12 CO 3 4H 2 The isoelectric point of O is 9.9. 0.2% dilute hydrochloric acid solution was added dropwise to the above four slurries under stirring condition, so that the pH values of the four slurries were 10.5, 10.0, 9.5 and 9 respectively. The tempe...
Embodiment 2
[0036] 129.4g ZnSO 4 ·7H 2 O and 50.0gAl 2 (SO 4 ) 3 18H 2 O was dissolved in deionized water to make a 300ml mixed salt solution, 38.4g NaOH was dissolved in 300ml water to make an alkali solution, and the two solutions were added to the full back-mixed liquid membrane reactor at the same time, and the obtained slurry was placed in a 2L flask under stirring conditions Heated to reflux, reacted for 6h to obtain Zn 6 al 2 (OH) 12 SO 4 4H 2 O slurry, cooled to room temperature, is divided into 4 parts, each part contains about 5g of product, and the pH value of the measured slurry is 10.5. Determination of Zn by DXD2II TV Microelectrophoresis Apparatus 6 al 2 (OH) 12 SO 4 4H 2 The isoelectric point of O is 9.7. A dilute sulfuric acid solution with a concentration of 0.2% was prepared and added dropwise to the above slurry under stirring conditions to adjust the pH of the system to 10.5, 10.0, 9.5 and 9 respectively. The temperature was raised to 80°C, and 0.25 g ...
Embodiment 3
[0041] 76.9g Mg(NO 3 ) 2 ·6H 2 O and 56.3g Al(NO 3 ) 3 9H 2 O was dissolved in deionized water to make a 500ml mixed salt solution, 36.0g NaOH was dissolved in 300ml water to make an alkaline solution, and the two solutions were simultaneously added to the full back-mixed liquid membrane reactor, and the obtained slurry was placed in a 2L flask under stirring conditions Heated to reflux, reacted for 6h to obtain Mg 4 al 2 (OH) 12 NO 3 4H 2 O slurry, cooled to room temperature, is divided into 4 parts, each part contains about 5g of product, and the pH value of the measured slurry is 10.2. Determination of Mg with DXD2II TV Microelectrophoresis Apparatus 4 al 2 (OH) 12 NO 3 4H 2 The isoelectric point of O is 9.4. A dilute sulfuric acid solution with a concentration of 0.1% was prepared and added dropwise to the above slurry under stirring conditions to adjust the pH of the system to 10.5, 10.0, 9.5 and 9 respectively. Raise the temperature to 80°C, add 0.2g of l...
PUM
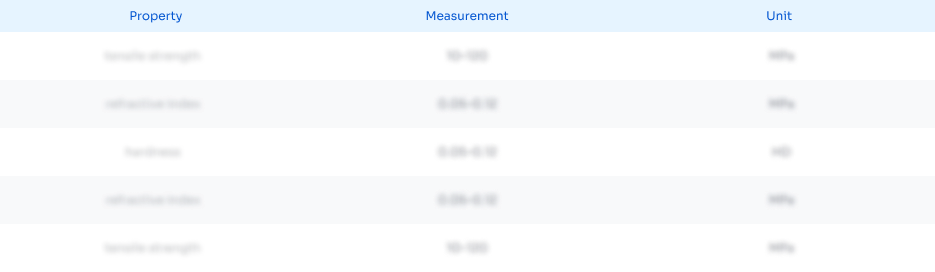
Abstract
Description
Claims
Application Information

- R&D
- Intellectual Property
- Life Sciences
- Materials
- Tech Scout
- Unparalleled Data Quality
- Higher Quality Content
- 60% Fewer Hallucinations
Browse by: Latest US Patents, China's latest patents, Technical Efficacy Thesaurus, Application Domain, Technology Topic, Popular Technical Reports.
© 2025 PatSnap. All rights reserved.Legal|Privacy policy|Modern Slavery Act Transparency Statement|Sitemap|About US| Contact US: help@patsnap.com