Raw material components and production method of diphenyl phosphorus chloride
A technology of diphenylphosphorus chloride and production method, which is applied in chemical instruments and methods, organic chemistry, compounds of Group 5/15 elements of the periodic table, etc. Long time and other problems, to achieve the effect of reducing raw material consumption, shortening reaction time, and reducing the discharge of three wastes
- Summary
- Abstract
- Description
- Claims
- Application Information
AI Technical Summary
Problems solved by technology
Method used
Image
Examples
Embodiment 1
[0027] The raw material component of a kind of diphenylphosphorus chloride of this embodiment, comprises the halide of active metal, benzene, phosphorus trichloride, organic solvent, catalyst, wherein by mass parts, active metal sodium 0.8 part, benzene 1 part of halide, 1 part of phosphorus trichloride, 1 part of organic solvent, 0.03 part of catalyst;
[0028] The production method of present embodiment diphenyl phosphorus chloride is as follows:
[0029] In the production method of the following examples, take the example of active metal sodium, benzene halide chlorobenzene, organic solvent xylene, and catalyst aluminum trichloride;
[0030] 1. Under the protection conditions of anhydrous, anaerobic and nitrogen, put 1 part of xylene and 0.8 part of metal sodium into the dispersion kettle according to the mass parts, close the pot mouth, open the jacket and steam to 90-130 ℃, stir and disperse sodium metal at 300-2500 rpm for 2-40 minutes to disperse the sodium into partic...
Embodiment 2
[0037] Embodiment 2 The difference between a kind of diphenyl phosphorus chloride of this embodiment and embodiment 1 is that,
[0038] The raw material component of a kind of diphenylphosphorous chloride of this embodiment, comprises the halide of active metal, benzene, phosphorus trichloride, organic solvent, catalyst, wherein according to mass parts, active metal 1.5 parts, halogenated benzene 4 parts of compound, 3 parts of phosphorus trichloride, 8 parts of organic solvent, 0.1 part of catalyst;
[0039] The difference between the production method of the present embodiment diphenyl phosphorus chloride and embodiment 1 is,
[0040] 1. Under the protection conditions of anhydrous, oxygen and nitrogen, mix 8 parts of xylene and 1.5 parts of sodium metal into the dispersion kettle according to the mass parts, heat to 90-130 ℃, and use 300-2500 rpm Stir and disperse the sodium metal at a high stirring speed for 2 to 40 minutes to disperse the sodium into particles below 120 ...
Embodiment 3
[0044] Embodiment 3: The difference between a kind of diphenyl phosphorus chloride of the present embodiment and embodiment 1 is,
[0045] The raw material component of a kind of diphenylphosphorous chloride of this embodiment, comprises the halide of active metal, benzene, phosphorus trichloride, organic solvent, catalyst, wherein according to mass parts, active metal 1.0 parts, halogenated benzene 2 parts of compound, 1.5 parts of phosphorus trichloride, 2 parts of organic solvent, 0.05 part of catalyst;
[0046] The difference between the production method of the present embodiment diphenyl phosphorus chloride and embodiment 1 is,
[0047] 1. Under the protection conditions of anhydrous, oxygen and nitrogen, mix 2 parts of xylene and 1.0 part of metal sodium into the dispersion kettle according to the mass parts, heat to 90-130 ℃, and use 300-2500 rpm Stir and disperse the sodium metal at a high stirring speed for 2 to 40 minutes to disperse the sodium into particles below...
PUM
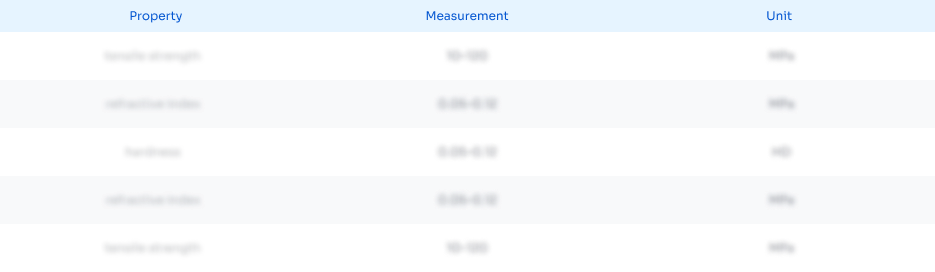
Abstract
Description
Claims
Application Information

- Generate Ideas
- Intellectual Property
- Life Sciences
- Materials
- Tech Scout
- Unparalleled Data Quality
- Higher Quality Content
- 60% Fewer Hallucinations
Browse by: Latest US Patents, China's latest patents, Technical Efficacy Thesaurus, Application Domain, Technology Topic, Popular Technical Reports.
© 2025 PatSnap. All rights reserved.Legal|Privacy policy|Modern Slavery Act Transparency Statement|Sitemap|About US| Contact US: help@patsnap.com