Method for processing spherical closing-in of thin-wall alloy steel delivery tube and special-purpose hob cutter
A technology of alloy steel and hob, applied in the field of mechanical processing, can solve the problems of high price and increase manufacturing cost, and achieve the effect of reducing processing cost
- Summary
- Abstract
- Description
- Claims
- Application Information
AI Technical Summary
Problems solved by technology
Method used
Image
Examples
Embodiment 1
[0020] Example 1. Processing outer diameter D=25.4mm catheter spherical closing, wall thickness 1mm, the section arc radius r=12.8mm of the working surface 5 of the roller 2 of the special-purpose hob used.
[0021] The processing steps are:
[0022] 1. Clamping; clamp one end of the pipe to be processed on the lathe chuck, and the extension length is 100mm;
[0023] 2. Tool setting; make the rear edge A of the arc working surface of the special hob roller be located at the position 12mm behind the port of the pipe material to be processed;
[0024] 3. Heating the pipe material; use an acetylene gas torch to heat the end of the pipe material to be processed, the length of the heating area is 20mm, and the heating temperature is 920°C;
[0025] 4. Vertical spinning; the speed of the lathe is 550r / min, the total amount of feed is 5mm, and the feed speed is 0.08mm / r;
[0026] 5. Horizontal spinning; the total amount of feed is 0.4D, the lathe speed is 550r / min, the feed speed ...
Embodiment 2
[0027] Example 2. Processing outer diameter D=28mm catheter spherical closing, wall thickness 1.5mm, the section arc radius r=13.9mm of the working surface 5 of the roller 2 of the special-purpose hob used.
[0028] The processing steps are:
[0029] 1. Clamping; clamp one end of the pipe to be processed on the lathe chuck, and the extension length is 110mm;
[0030] 2. Tool setting; make the rear edge A of the arc working surface of the special hob roller be located at the position 13mm behind the port of the pipe material to be processed;
[0031] 3. Heating the pipe material; use the induction coil to heat the end of the pipe material to be processed, the length of the heating area is 22mm, and the heating temperature is 960°C;
[0032] 4. Vertical spinning; the speed of the lathe is 500r / min, the total amount of feed is 6mm, and the feed speed is 0.10mm / r;
[0033] 5. Horizontal spinning; the total amount of feed is 0.45D, the lathe speed is 500r / min, the feed speed is ...
Embodiment 3
[0034] Example 3. Processing outer diameter D=22mm catheter spherical closing, wall thickness 0.8mm, the section arc radius r=11.15mm of the working surface 5 of the roller 2 of the special-purpose hob used.
[0035] The processing steps are:
[0036] 1. Clamping; clamp one end of the pipe to be processed on the lathe chuck, and the extension length is 90mm;
[0037] 2. Tool setting; make the rear edge A of the arc working surface of the special hob roller be located at the position 11mm behind the port of the pipe material to be processed;
[0038] 3. Heating the pipe material; use an acetylene gas torch to heat the end of the pipe material to be processed, the length of the heating area is 15mm, and the heating temperature is 980°C;
[0039] 4. Vertical spinning; the speed of the lathe is 600r / min, the total amount of feed is 5mm, and the feed speed is 0.12mm / r;
[0040] 5. Horizontal spinning; the total amount of feed is 0.5D, the lathe speed is 600r / min, the feed speed ...
PUM
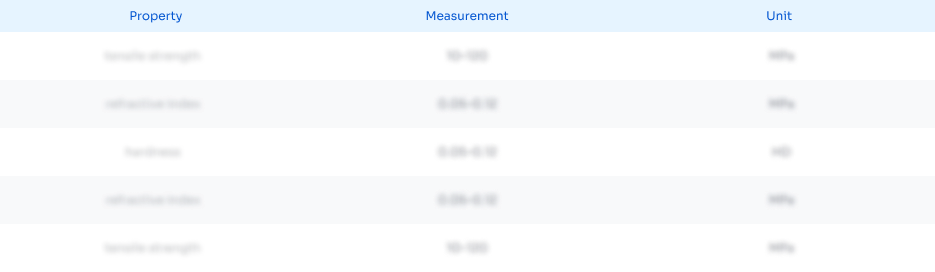
Abstract
Description
Claims
Application Information

- R&D
- Intellectual Property
- Life Sciences
- Materials
- Tech Scout
- Unparalleled Data Quality
- Higher Quality Content
- 60% Fewer Hallucinations
Browse by: Latest US Patents, China's latest patents, Technical Efficacy Thesaurus, Application Domain, Technology Topic, Popular Technical Reports.
© 2025 PatSnap. All rights reserved.Legal|Privacy policy|Modern Slavery Act Transparency Statement|Sitemap|About US| Contact US: help@patsnap.com