Catalyst module edge hardening liquid with activity
A catalyst module and hardening solution technology, which is applied in the direction of catalyst activation/preparation, physical/chemical process catalysts, chemical instruments and methods, etc., can solve the problems of reduced service life of catalysts, non-protrusive catalyst wear, and end wear, etc., to achieve improved Effects of overall service life, improved module strength, and improved catalyst life
- Summary
- Abstract
- Description
- Claims
- Application Information
AI Technical Summary
Problems solved by technology
Method used
Examples
Embodiment 1
[0010] Get the sodium metasilicate of 24g and 1g aluminum sulfate, the ammonium metavanadate of 16g add in the water of 59g and stir to form hardening liquid, promptly in this hardening liquid, sodium metasilicate accounts for 24% by weight percentage content, ammonium metavanadate It accounts for 6% by weight in the hardening solution.
[0011] A 300MW coal-fired unit flue gas denitrification project, the dust content in the flue gas is 40g / Nm 3 , the concentration of nitrogen oxides is 400mg / Nm 3 , the flue gas temperature is 400°C, and the hardening process of the SCR honeycomb catalyst product is as follows:
[0012] Take two batches of honeycomb catalyst monomers that have been formed and dried in the same quantity. One batch of honeycomb catalyst monomers at both ends of the module are soaked in hardening solution at a distance of 15 mm from the end. Curing: After curing, the catalyst is sent to a kiln above 500°C for calcination, so that the hardening liquid can be ...
Embodiment 2
[0019] Get the sodium metasilicate of 40g, the aluminum sulfate of 3g, the ferrous sulfate of 1g and add in the water of 56g and stir to form hardening liquid, promptly in this hardening liquid, sodium metasilicate accounts for 40% by weight percentage content, ferrous sulfate is in The hardening solution accounts for 1% by weight.
[0020] A 300MW coal-fired unit flue gas denitrification project, the dust content in the flue gas is 60g / Nm 3 , the concentration of nitrogen oxides is 400mg / Nm 3 , the flue gas temperature is 370°C, and the hardening process of the SCR honeycomb catalyst product is as follows:
[0021] Take two batches of honeycomb catalyst monomers that have been formed and dried in the same quantity. One batch of honeycomb catalyst monomers at both ends of the module are soaked in hardening solution at a distance of 35 mm from the end. Curing: After curing, the catalyst is sent to a kiln above 500°C for calcination, so that the hardening liquid can be convert...
Embodiment 3
[0026] Get 32g of sodium metasilicate, 2g of aluminum sulfate, and 5g of manganese nitrate and add them into 61g of water and stir to form a hardening solution, that is, sodium metasilicate accounts for 32% by weight in the hardening solution, and manganese nitrate 5% by weight in the liquid.
[0027] A 600MW coal-fired unit flue gas denitrification project, the dust content in the flue gas is 50g / Nm 3 , the concentration of nitrogen oxides is 400mg / Nm 3 , the flue gas temperature is 300°C, and the hardening process of the SCR honeycomb catalyst product is as follows:
[0028] Take two batches of honeycomb catalyst monomers that have been formed and dried in the same quantity. One batch of honeycomb catalyst monomers at both ends of the module are soaked in hardening solution at a distance of 25mm from the end. Curing: After curing, the catalyst is sent to a kiln above 500°C for calcination, so that the hardening liquid can be converted into effective hardening and active co...
PUM
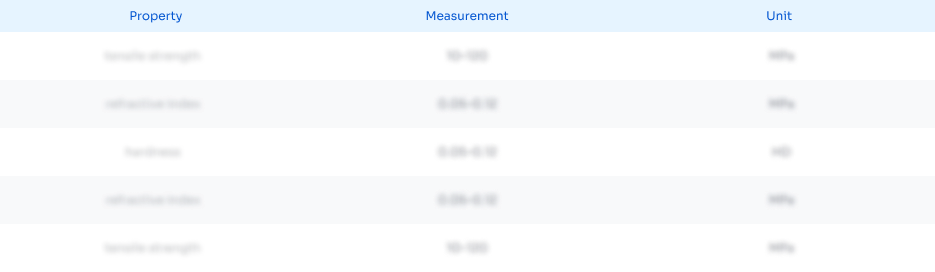
Abstract
Description
Claims
Application Information

- Generate Ideas
- Intellectual Property
- Life Sciences
- Materials
- Tech Scout
- Unparalleled Data Quality
- Higher Quality Content
- 60% Fewer Hallucinations
Browse by: Latest US Patents, China's latest patents, Technical Efficacy Thesaurus, Application Domain, Technology Topic, Popular Technical Reports.
© 2025 PatSnap. All rights reserved.Legal|Privacy policy|Modern Slavery Act Transparency Statement|Sitemap|About US| Contact US: help@patsnap.com