Method for preparing high performance yttrium oxide material
A technology of yttrium oxide and raw materials, which is applied in the field of preparing high-performance yttrium oxide materials, can solve the problems of high sintering temperature, poor thermal shock resistance, and low strength, and achieve the effects of less equipment investment, improved production efficiency, and simple process
- Summary
- Abstract
- Description
- Claims
- Application Information
AI Technical Summary
Problems solved by technology
Method used
Image
Examples
Embodiment 1
[0030] Use yttrium oxide powder with an average particle size of 1 μm as raw material, add 1 mol% additive powder with an average particle size of 0.5 μm, use an agate mortar to fully mix the raw materials, and use a metal mold to form under a pressure of 100 MPa. Then place the sample on MoSi 2 The microstructure can be obtained by heating at 1600°C for 5 hours in a resistance furnace, such as figure 1 Excellent rod-shaped grain-reinforced high-strength yttrium oxide material shown.
Embodiment 2
[0032] Add 5 mol% additives to yttrium nitrate, then add the mixed reagent into the alcohol aqueous solution with alcohol-water ratio of 5:1 and dissolve completely. Under the condition of vigorous stirring, slowly heat to 75°C and keep for a period of time, then slowly add ammonia water dropwise until the pH value of the solution is greater than 9. After cleaning with deionized water and alcohol, the obtained material is completely dried and then calcined at 400° C. to obtain nanoscale powder. The powder is molded under a pressure of 100 MPa with a metal mold. Then place the sample on MoSi 2 The microstructure can be obtained by heating at 1500°C for 2 hours in a resistance furnace, such as figure 2 A long columnar grain reinforced high strength yttrium oxide material is shown.
PUM
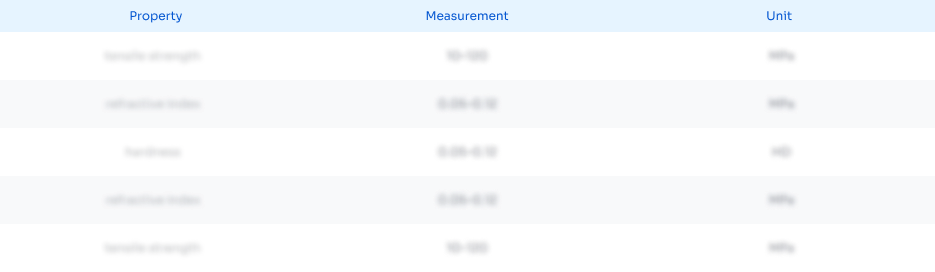
Abstract
Description
Claims
Application Information

- R&D Engineer
- R&D Manager
- IP Professional
- Industry Leading Data Capabilities
- Powerful AI technology
- Patent DNA Extraction
Browse by: Latest US Patents, China's latest patents, Technical Efficacy Thesaurus, Application Domain, Technology Topic, Popular Technical Reports.
© 2024 PatSnap. All rights reserved.Legal|Privacy policy|Modern Slavery Act Transparency Statement|Sitemap|About US| Contact US: help@patsnap.com