Method for preparing maleic anhydride-alkyl vinyl ether co-polymer
A technology of alkyl vinyl ether and methyl vinyl ether, which is applied in the field of organic chemical production and can solve the problems of high toxicity of solvents, etc.
- Summary
- Abstract
- Description
- Claims
- Application Information
AI Technical Summary
Problems solved by technology
Method used
Examples
Embodiment 1
[0012] Dissolve 98.0g maleic anhydride in 200g mixed solvent (the ratio of n-hexane and methyl ethyl ketone is 4:1, the same below), put it into a 1000mL high-pressure reactor with a stirring paddle, start stirring under the protection of nitrogen, and raise the temperature to 81°C , within 1 hour, a mixture of 34g mixed solvent, 55.1g methyl vinyl ether, 2.85g isobutyl vinyl ether, 0.04g peroxydicarbonate bis(2-ethyl-hexyl) ester was added dropwise to the reaction Kettle, maintained at 81 ° C for 7 hours of polymerization reaction to obtain a slurry copolymer solution, filtered and vacuum dried to finally obtain 150.3 g of white polymer powder with a yield of 96.4%. The analysis test results are shown in Table 1.
Embodiment 2
[0014] Dissolve 98.0g maleic anhydride in 200g mixed solvent (the ratio of n-hexane and methyl ethyl ketone is 4:1, the same below), put it into a 1000mL autoclave with a stirring paddle, start stirring under the protection of nitrogen, and raise the temperature to 85°C , within 1 hour, a mixture of 160g mixed solvent, 55.1g methyl vinyl ether, 5.0g isobutyl vinyl ether, and 0.16g peroxydicarbonate bis(2-ethyl-hexyl) ester was added dropwise to the reaction The kettle was kept at 85° C. for 6 hours for polymerization reaction to obtain a slurry copolymer solution, which was filtered and vacuum-dried to finally obtain 150.3 g of white polymer powder with a yield of 95.1%. The analysis test results are shown in Table 1.
Embodiment 3
[0016] Dissolve 98.0g maleic anhydride in 200g mixed solvent (the ratio of n-hexane to methyl ethyl ketone is 3:1, the same below), put it into a 1000mL autoclave with a stirring paddle, start stirring under the protection of nitrogen, and raise the temperature to 90°C , within 1 hour, a mixture of 160g mixed solvent, 55.1g methyl vinyl ether, 5.0g isobutyl vinyl ether, and 0.16g peroxydicarbonate bis(2-ethyl-hexyl) ester was added dropwise to the reaction The kettle was kept at 90° C. for 5 hours for polymerization reaction to obtain a slurry copolymer solution, which was filtered and vacuum-dried to finally obtain 148.1 g of white polymer powder with a yield of 93.7%. The analysis test results are shown in Table 1.
PUM
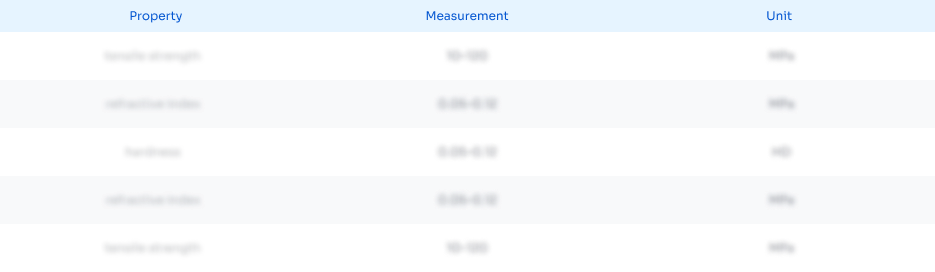
Abstract
Description
Claims
Application Information

- R&D Engineer
- R&D Manager
- IP Professional
- Industry Leading Data Capabilities
- Powerful AI technology
- Patent DNA Extraction
Browse by: Latest US Patents, China's latest patents, Technical Efficacy Thesaurus, Application Domain, Technology Topic, Popular Technical Reports.
© 2024 PatSnap. All rights reserved.Legal|Privacy policy|Modern Slavery Act Transparency Statement|Sitemap|About US| Contact US: help@patsnap.com