Process for preparing alumina carrier
A technology of alumina carrier and alumina, which is applied in the field of catalysis, can solve the problems of general carrier strength and carrier inability to meet the requirements, and achieve the effect of good mechanical strength, good mechanical strength and good stability
- Summary
- Abstract
- Description
- Claims
- Application Information
AI Technical Summary
Problems solved by technology
Method used
Examples
Embodiment 1
[0016] ① Take 300g Al 2 o 3 ·H 2 O, heat treatment at 200°C to 300°C, the heat treatment time is 1.5h to 2h; ②Add 9g of graphite and 150g of water to the heat-treated alumina and knead evenly. ③Pellet the kneaded uniform material into particles with a particle diameter of about 1.2mm, and dry at 120°C for 24 hours; ④The dried particles are compressed into cylindrical particles of Φ3×3mm by a tablet machine; ⑤The tablets are roasted at 850°C Obtain the required carrier I.
Embodiment 2
[0018] ① Take 300g Al 2 o 3 ·H 2 O, conduct heat treatment at 200°C to 300°C, and the heat treatment time is 1.5h to 2h; ②Add 9g of stearic acid and 150g of water to the heat-treated alumina, and knead evenly. ③Granulate the uniformly kneaded material into particles with a particle size of about 1.2mm, and dry at 120°C for 24 hours; ④The dried particles are compressed into cylindrical particles of Φ3×3mm by a tablet machine; ⑤The tablets are roasted at 750°C The desired vector II is obtained.
Embodiment 3
[0020] The above-mentioned carriers were tested for their physical and chemical properties, and the results are shown in the table below:
[0021]
[0022] The test results show that the carrier prepared by the invention has good mechanical strength, suitable specific surface and pore structure.
PUM
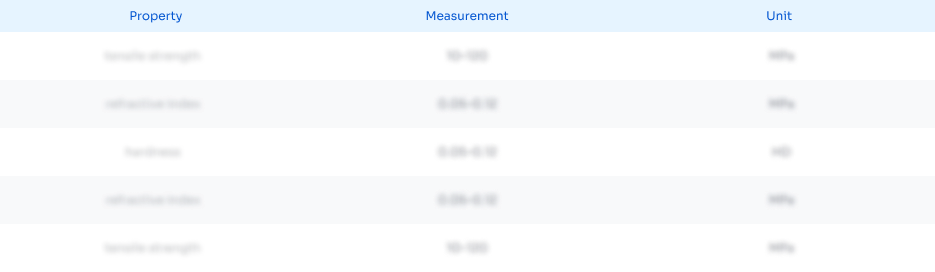
Abstract
Description
Claims
Application Information

- R&D Engineer
- R&D Manager
- IP Professional
- Industry Leading Data Capabilities
- Powerful AI technology
- Patent DNA Extraction
Browse by: Latest US Patents, China's latest patents, Technical Efficacy Thesaurus, Application Domain, Technology Topic, Popular Technical Reports.
© 2024 PatSnap. All rights reserved.Legal|Privacy policy|Modern Slavery Act Transparency Statement|Sitemap|About US| Contact US: help@patsnap.com