Method for preparing composite floor core material using bark of dahurian larch as raw material
A composite floor, pine bark technology, applied in the pretreatment of molding materials, wood treatment, flat products, etc., can solve the problem of poor thermal conductivity, shock absorption and sound insulation performance, low utilization rate of larch bark, low thermal insulation performance, etc. problem, to achieve the effect of low thermal conductivity, good thermal insulation performance, good shock absorption and sound insulation performance
- Summary
- Abstract
- Description
- Claims
- Application Information
AI Technical Summary
Problems solved by technology
Method used
Examples
specific Embodiment approach 1
[0010] Embodiment 1: The preparation method of the composite floor core material of the present embodiment is realized by the following steps:
[0011] Step 1, using a disc chipper and a ring planer to plan the larch bark into larch bark scraps with a length of 10-30 mm, a width of 3-10 mm and a thickness of 0.2-0.5 mm;
[0012] Step 2, using drying equipment to dry the larch bark fragments obtained in step 1 to a moisture content of 3% to 5%;
[0013] Step 3, according to the density of the floor core board 0.85 ~ 0.95g / cm 3 Calculate, the application amount of phenolic resin glue is 8%~10% (relative to the amount of absolute dry shavings) of the larch bark scrap by weight percentage, put the phenolic resin glue and larch bark scrap in the glue mixer and mix evenly;
[0014] Step 4: Use a paving machine to pave the bark scraps after sizing in a single layer structure, and then press them on the press with a pressure of 2.5-3.0 MPa and a temperature of 190-210 ° C. The pressi...
specific Embodiment approach 2
[0015] Specific embodiment two: the difference between this embodiment and specific embodiment one is that in step one, larch bark utilizes a disc chipper and a ring planer to pulverize to a length of 20 mm, a width of 6 mm and a thickness of 0.3 mm. Shredded larch bark. Other steps are the same as in the first embodiment.
specific Embodiment approach 3
[0016] Embodiment 3: The difference between this embodiment and Embodiment 1 is that in step 2, the crushed material is dried to a moisture content of 4%. Other steps are the same as in the first embodiment.
PUM
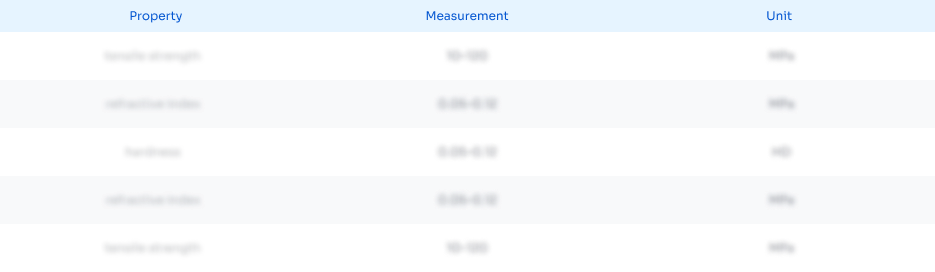
Abstract
Description
Claims
Application Information

- R&D
- Intellectual Property
- Life Sciences
- Materials
- Tech Scout
- Unparalleled Data Quality
- Higher Quality Content
- 60% Fewer Hallucinations
Browse by: Latest US Patents, China's latest patents, Technical Efficacy Thesaurus, Application Domain, Technology Topic, Popular Technical Reports.
© 2025 PatSnap. All rights reserved.Legal|Privacy policy|Modern Slavery Act Transparency Statement|Sitemap|About US| Contact US: help@patsnap.com