Polyester knitwear fabric and method of processing the same
A processing method and polyester technology, which is applied in the processing of knitted polyester fabrics, and in the field of knitted polyester fabrics, can solve the problems of soft hand feeling, large deviation of door width and weight, waste, etc., and achieve excellent warmth and breathability, good heat absorption, The effect of small material loss
- Summary
- Abstract
- Description
- Claims
- Application Information
AI Technical Summary
Problems solved by technology
Method used
Image
Examples
Embodiment 1
[0025] A) Raw material preparation, select 75D / 144F polyester superfine denier fiber as the surface structure, select 100D / 36F ordinary polyester fiber as the bottom structure, wherein, the content of polyester superfine denier fiber accounts for 75% of the total composition, while ordinary polyester fiber content of 25% of the total ingredients;
[0026] B) weft knitting, the 75D / 144F polyester superfine denier polyester fiber and 100D / 36F polyester fiber selected in step A) are put into the weft knitting terry machine weft knitting, preferably but not limited to the weft knitting terry machine A large circular knitting machine with a brand name of Li Kemao and a specification of 30 inches and 24 needles produced in Taiwan, China, can obtain white gray cloth after warp and weft knitting;
[0027] C) opening width, napping, the white gray cloth obtained in step B) is first opened by the opening width machine and then single-sided napping is carried out on the loop surface. The...
Embodiment 2
[0032] A) Raw material preparation, select 75D / 144F polyester superfine denier fiber as the surface structure, select 125D / 36F ordinary polyester fiber as the bottom structure, wherein, the content of polyester superfine denier fiber accounts for 70% of the total composition, while ordinary polyester fiber content of 30% of the total ingredients;
[0033] B) weft knitting, the 75D / 144F polyester superfine denier polyester fiber and 125D / 36F polyester fiber selected in step A) are put into the weft knitting machine weft knitting, preferably but not limited to the weft knitting machine A large circular knitting machine with a brand name of Li Kemao and a specification of 30 inches and 24 needles produced in Taiwan, China, can obtain white gray cloth after warp and weft knitting;
[0034] C) opening width, napping, the white gray cloth obtained in step B) is first opened by the opening width machine and then single-sided napping is carried out on the loop surface. The used machin...
Embodiment 3
[0039] A) Raw material preparation, select 150D / 288F polyester superfine denier fiber as the surface structure, select 100D / 36F ordinary polyester fiber as the bottom structure, wherein, the content of polyester superfine denier fiber accounts for 80% of the total composition, and ordinary polyester fiber content of 20% of the total ingredients;
[0040] B) weft knitting, the 150D / 288F polyester superfine denier polyester fiber and 100D / 36F polyester fiber selected in step A) are put into the weft knitting terry machine weft knitting, preferably but not limited to the weft knitting terry machine A large circular knitting machine with a brand name of Li Kemao and a specification of 30 inches and 24 needles produced in Taiwan, China, can obtain white gray cloth after warp and weft knitting;
[0041] C) opening width, napping, the white gray cloth that step B) is obtained is first carried out double-sided napping after opening the width of the opening width machine, and the machi...
PUM
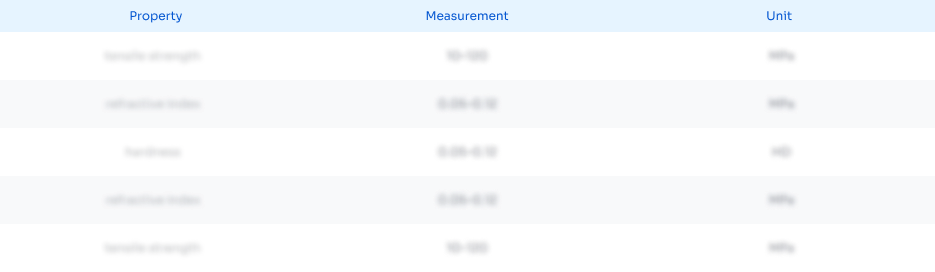
Abstract
Description
Claims
Application Information

- Generate Ideas
- Intellectual Property
- Life Sciences
- Materials
- Tech Scout
- Unparalleled Data Quality
- Higher Quality Content
- 60% Fewer Hallucinations
Browse by: Latest US Patents, China's latest patents, Technical Efficacy Thesaurus, Application Domain, Technology Topic, Popular Technical Reports.
© 2025 PatSnap. All rights reserved.Legal|Privacy policy|Modern Slavery Act Transparency Statement|Sitemap|About US| Contact US: help@patsnap.com