Rolling oil composition for 12-roller reversing mill
A technology for rolling oil and composition, applied in the directions of lubricating composition, petroleum industry, base material, etc., can solve the problems of affecting the cleanliness of rolling mill, inconvenient use, poor rust prevention, etc., and achieve remarkable technological progress and outstanding features, The effect of obvious economic and social benefits
- Summary
- Abstract
- Description
- Claims
- Application Information
AI Technical Summary
Problems solved by technology
Method used
Examples
Embodiment 1
[0061] Add 9.6g of 150SN mechanical oil and 9.6g of 500SN mechanical oil to the blending kettle, raise the temperature to 60-70°C, add 1.5g of antioxidant 2,6-di-tert-butyl p-cresol, and copolymerize defoamer acrylate and ether T911 10.1g, stir until the additive dissolves; cool down to 60°C, add 25g of pentaerythritol oleic acid, stearic acid, dimer acid mixed ester, trimethylolpropane coconut oleic acid, palmitoleic acid, oleic acid 40g of mixed acid ester, stir evenly; at 50°C, add 2g of phosphorus-containing extreme pressure antiwear agent C12 fatty alcohol polyoxyethylene ether (3) phosphate ester, 1.2g of rust inhibitor cyclohexylamine, stir for 30 minutes, and finally add Emulsifier Pluronic L12 16g, Tween-804g, and sulfur-containing extreme pressure antiwear agent vulcanized olefin cottonseed oil T405A 1g, stirred for 30 minutes to obtain 100g of the composition of the present invention.
Embodiment 2
[0063] Add 6.4g of 25# transformer oil and 12g of 500SN mechanical oil to the blending kettle, raise the temperature to 60-70°C, add 1g of antioxidant 2,6-di-tert-butyl-p-cresol, N-phenyl-a-naphthylamine 0.5g, defoamer acrylate and ether copolymer T911 0.1g, stir until the additive is dissolved; cool down to 60°C, add pentaerythritol oleic acid, stearic acid, dimer acid mixed ester 20g, trimethylolpropane 45g of mixed esters of coconut oleic acid, palmitoleic acid and oleic acid, and stir evenly; at 50°C, add 2g of phosphorus-containing extreme pressure antiwear agent C12 fatty alcohol phosphate, and 1.5g of rust inhibitor cyclohexylamine, and stir After 30 minutes, 15.5 g of emulsifier Pluronic L12, 5.5 g of NP-10, and 0.5 g of sulfurized isobutylene T321, a sulfur-containing extreme pressure and antiwear agent, were finally added, and stirred for 30 minutes to obtain 100 g of the composition of the present invention.
Embodiment 3
[0065] Add 7.6g of 40# transformer oil and 7.6g of 500SN mechanical oil to the blending kettle, raise the temperature to 60-70°C, add 1g of antioxidant 2,6-di-tert-butyl-p-cresol, N-phenyl-a-naphthalene Amine 1g, defoamer acrylate and ether copolymer T911 0.1g, stir until the additive is dissolved; cool down to 60°C, add pentaerythritol oleic acid, stearic acid, dimer acid mixed ester 33g, trimethylolpropane 35g of mixed acid ester of coconut oil and oleic acid, stir evenly; at 50°C, add phosphorus-containing extreme pressure antiwear agent C12 fatty alcohol polyoxyethylene ether (9) phosphate ester 1.5g, and rust inhibitor cyclohexylamine 0.7g, stirred for 30 minutes, finally added emulsifier Pluronic L12 16g, NP-105g, and sulfurized extreme pressure antiwear agent vulcanized lard 1.5g, stirred for 30 minutes to obtain 100g of the composition of the present invention.
PUM
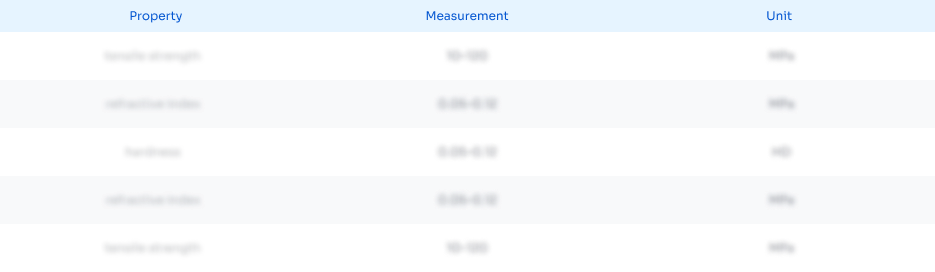
Abstract
Description
Claims
Application Information

- R&D
- Intellectual Property
- Life Sciences
- Materials
- Tech Scout
- Unparalleled Data Quality
- Higher Quality Content
- 60% Fewer Hallucinations
Browse by: Latest US Patents, China's latest patents, Technical Efficacy Thesaurus, Application Domain, Technology Topic, Popular Technical Reports.
© 2025 PatSnap. All rights reserved.Legal|Privacy policy|Modern Slavery Act Transparency Statement|Sitemap|About US| Contact US: help@patsnap.com