Molding method for high-strength high-modulus aluminum based composite material
A technology of aluminum-based composite materials and forming methods, which is applied in the field of material processing, can solve problems such as being unsuitable for forming high-strength and high-modulus aluminum-based composite materials, and achieve low residual stress levels of components, stable forming quality, and high accuracy. Effect
- Summary
- Abstract
- Description
- Claims
- Application Information
AI Technical Summary
Problems solved by technology
Method used
Image
Examples
Embodiment 1
[0028] The composition mass percentage of aluminum matrix composite material is Zn 8.0wt%, Mg 2.3wt%, Cu 2.3wt%, Zr 0.15wt%, Mn≤0.05wt%, Cr≤0.04wt%, TiB 2 10wt%, the balance is Al.
[0029] Process: First, the aluminum matrix composite material plate is subjected to solution treatment at 460°C / 2h, quenched, and the mold and the actual required parts are designed with an additional 5% deformation to compensate for the springback of the aluminum matrix composite material after unloading. A high-temperature rubber gasket is provided at the junction of the aluminum-based composite material plate, and high-vacuum sealing grease is applied to vacuumize the cavity between the aluminum-based composite material plate and the molding surface of the mold to 1×10 -9 MPa, put the aluminum-based composite material plate and the mold in the autoclave, the pressure of 200 MPa generated by the autoclave device, the pressure evenly acts on the surface of the aluminum-based composite material p...
Embodiment 2
[0031] The composition mass percentage of aluminum matrix composite material is Zn 8.0wt%, Mg 2.3wt%, Cu 2.3wt%, Zr 0.15wt%, Mn≤0.05wt%, Cr≤0.04wt%, TiB 2 10wt%, the balance is Al.
[0032] Process: First, the aluminum matrix composite material plate is subjected to solution treatment at 550°C / 15min, quenched, and the mold and the actual required parts are designed with an additional 1% deformation to compensate for the springback of the aluminum matrix composite material after unloading. A high-temperature rubber gasket is provided at the junction of the aluminum-based composite material plate, and high-vacuum sealing grease is applied to vacuumize the cavity between the aluminum-based composite material plate and the molding surface of the mold to 1×10 -7 MPa, put the aluminum-based composite material plate and the mold in the autoclave, the pressure of 150MPa generated by the autoclave device, the pressure evenly acts on the surface of the aluminum-based composite material...
Embodiment 3
[0034] The composition mass percentage of aluminum matrix composite material is Zn 8.0wt%, Mg 2.3wt%, Cu 2.3wt%, Zr 0.15wt%, Mn≤0.05wt%, Cr≤0.04wt%, TiB 2 10wt%, the balance is Al.
[0035] Process: First, the aluminum matrix composite material plate is subjected to solution treatment at 450°C / 5h, quenched, and the mold and the actual required parts are designed with an additional 20% deformation to compensate for the springback of the aluminum matrix composite material after unloading. A high-temperature rubber gasket is provided at the junction of the aluminum-based composite material plate, and a high-vacuum sealing grease is applied to vacuumize the cavity between the aluminum-based composite material plate and the molding surface of the mold to 1×10 -12MPa, put the aluminum-based composite material plate and the mold in the autoclave, the pressure of 500 MPa generated by the autoclave device, the pressure evenly acts on the surface of the aluminum-based composite materia...
PUM
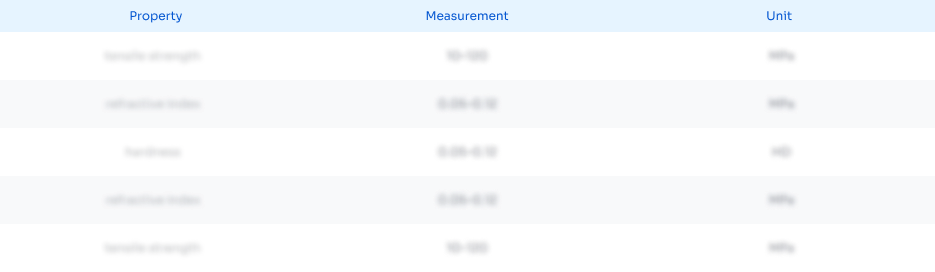
Abstract
Description
Claims
Application Information

- R&D Engineer
- R&D Manager
- IP Professional
- Industry Leading Data Capabilities
- Powerful AI technology
- Patent DNA Extraction
Browse by: Latest US Patents, China's latest patents, Technical Efficacy Thesaurus, Application Domain, Technology Topic, Popular Technical Reports.
© 2024 PatSnap. All rights reserved.Legal|Privacy policy|Modern Slavery Act Transparency Statement|Sitemap|About US| Contact US: help@patsnap.com