Arc welding robot control system and method thereof
A technology for arc welding and control devices, applied in arc welding equipment, computer control, program control, etc., can solve the problems of inconsistent timing, uneven thickness of weld bead, etc., to reduce the influence of delay, prevent uneven thickness, The effect of correct arc welding
- Summary
- Abstract
- Description
- Claims
- Application Information
AI Technical Summary
Problems solved by technology
Method used
Image
Examples
Embodiment Construction
[0023] (Outline of control device)
[0024] Hereinafter, embodiments of the present invention will be described in detail with reference to appropriate drawings. The outline of the control device will be described with reference to FIG. 1 . (a) is a configuration diagram showing the outline of an arc welding system including the control device of the present invention, and (b) is an enlarged view of a workpiece and a welding line in the present invention. (a) of FIG. 1 shows a control device (control device of an arc welding robot) 1 , an arc welding robot 2 , a teaching pendant type button table 4 , a welding torch 9 , and a workpiece W. As shown in FIG. In addition, (b) of FIG. 1 shows a workpiece|work W and a weld bead B. As shown in FIG.
[0025] The control device 1 controls the arc welding robot 2 based on commands input from the teaching pendant 4 and the teaching program, and changes the welding conditions of the arc welding robot 2 . In addition, the control device...
PUM
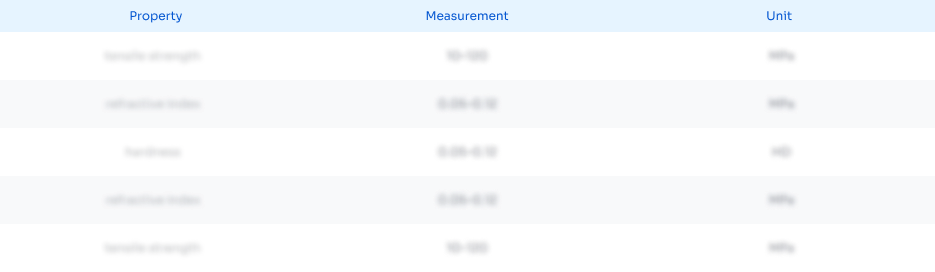
Abstract
Description
Claims
Application Information

- R&D
- Intellectual Property
- Life Sciences
- Materials
- Tech Scout
- Unparalleled Data Quality
- Higher Quality Content
- 60% Fewer Hallucinations
Browse by: Latest US Patents, China's latest patents, Technical Efficacy Thesaurus, Application Domain, Technology Topic, Popular Technical Reports.
© 2025 PatSnap. All rights reserved.Legal|Privacy policy|Modern Slavery Act Transparency Statement|Sitemap|About US| Contact US: help@patsnap.com