Terrestrial heat composite floor and manufacturing method thereof
A technology of composite floor and manufacturing method, which is applied to manufacturing tools, building structures, floors, etc., can solve the problems of inconvenient construction, failure to meet use requirements, and limited use occasions, and achieve the effect of convenient construction
- Summary
- Abstract
- Description
- Claims
- Application Information
AI Technical Summary
Problems solved by technology
Method used
Image
Examples
Embodiment 1
[0045] Embodiment 1: A method for manufacturing a geothermal composite floor, comprising the following process steps:
[0046] Operation A, preparation panel; Its technological process comprises:
[0047] Step A1: select high-quality hardwood species oak as the raw material for the panel;
[0048] Step A2: Process the panel raw material into a 3mm thick sheet with planer and sawing machine processing equipment;
[0049] Step A3: sending the surface plate sheet produced in step A2 into a drying kiln for drying at a drying temperature of 55° C. and a drying time of 72 hours, so that it becomes a surface plate blank with a moisture content of 6%;
[0050] Step A4: Send the surface plate blank made in step A3 into a constant temperature and humidity balance warehouse and let it stand for 5 days to release the internal stress of the surface plate blank, so that the base material is balanced and stable, so as to prevent the floor from being affected by temperature and humidity duri...
Embodiment 2
[0074] Embodiment 2: A method for manufacturing a geothermal composite floor, comprising the following process steps:
[0075] Operation A, preparation panel; Its technological process comprises:
[0076] Step A1: select high-quality hardwood species oak as the raw material for the panel;
[0077] Step A2: Process the surface plate raw material into a sheet with a thickness of 4.5 mm by planing and sawing machine processing equipment;
[0078] Step A3: sending the surface plate sheet produced in step A2 into a drying kiln for drying at a drying temperature of 60° C. and a drying time of 72 hours to make it a surface plate blank with a moisture content of 8%;
[0079] Step A4: Send the surface plate blank made in step A3 into a constant temperature and humidity balance warehouse and let it stand for 6 days to release the internal stress of the surface plate blank, so that the base material is balanced and stable, so as to prevent the floor from being affected by temperature an...
Embodiment 3
[0101] Embodiment 3: A method for manufacturing a geothermal composite floor, comprising the following process steps:
[0102] Operation A, preparation panel; Its technological process comprises:
[0103] Step A1: Select high-quality hardwood species Quliu as the raw material for the panel;
[0104] Step A2: Process the panel raw material into a 6mm thick sheet with planer and sawing machine processing equipment;
[0105] Step A3: sending the surface plate sheet produced in step A2 into a drying kiln for drying at a drying temperature of 65° C. and a drying time of 72 hours, so that it becomes a surface plate blank with a moisture content of 10%;
[0106] Step A4: Put the panel blank made in step A3 into a constant temperature and humidity balance warehouse and let it stand for 7 days to release the internal stress of the panel blank, so that the base material is balanced and stable, so as to prevent the floor from being affected by temperature and humidity during use. Defor...
PUM
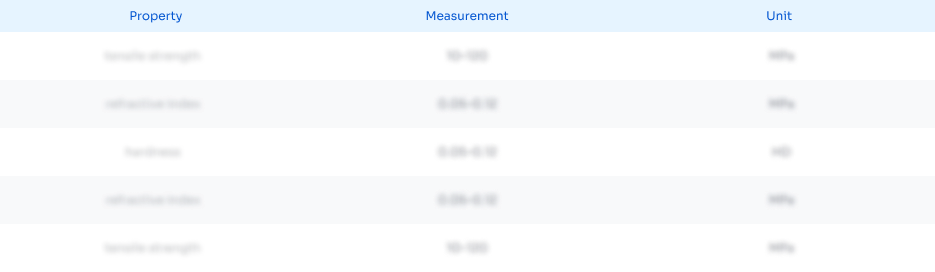
Abstract
Description
Claims
Application Information

- Generate Ideas
- Intellectual Property
- Life Sciences
- Materials
- Tech Scout
- Unparalleled Data Quality
- Higher Quality Content
- 60% Fewer Hallucinations
Browse by: Latest US Patents, China's latest patents, Technical Efficacy Thesaurus, Application Domain, Technology Topic, Popular Technical Reports.
© 2025 PatSnap. All rights reserved.Legal|Privacy policy|Modern Slavery Act Transparency Statement|Sitemap|About US| Contact US: help@patsnap.com