Device and method for casting composite hammer head
A technology of compound hammer head and hammer head is applied in the directions of casting molding equipment, casting mold, casting mold composition, etc., which can solve the problems of unreasonable casting structure, poor crack resistance reliability of hammer handle, poor wear resistance, etc., and achieve a simple casting method. The effect of easy operation, reliable crack resistance of hammer handle and low mechanical maintenance rate
- Summary
- Abstract
- Description
- Claims
- Application Information
AI Technical Summary
Problems solved by technology
Method used
Image
Examples
Embodiment Construction
[0011] like figure 1 The schematic diagram of the structure of the composite hammer head casting device of the present invention is shown, including a mold box 3 formed by compounding upper and lower templates, box clamps 32 are provided on both sides of the mold box 3, and a mold cavity matching the shape of the hammer head is provided in the mold box 3 31. The top of the cavity 31 is provided with a riser 35, the left and right sides of the cavity 31 are respectively provided with a runner I 33 and a runner II 34, the runner I 33 is connected to the bottom of the cavity 31 side, and the runner II 34 is connected to the cavity The top of the other side of 31, the other end openings of runner I 33 and runner II 34 are arranged on the top of mold box 3 .
[0012] The casting method of the above composite hammer head is as follows: pour the molten metal I into the runner I 33, the molten metal I flows into the bottom of the cavity 31 under the action of gravity, and when the mol...
PUM
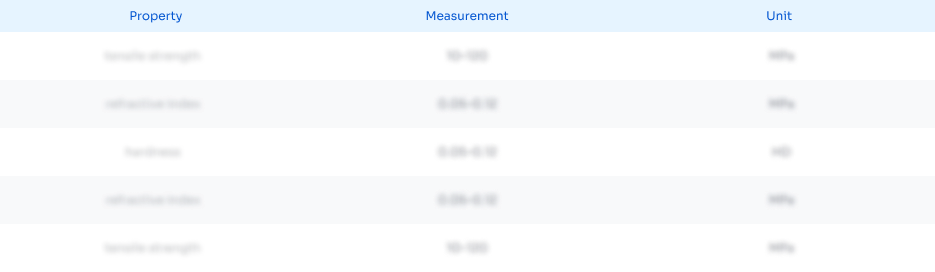
Abstract
Description
Claims
Application Information

- R&D
- Intellectual Property
- Life Sciences
- Materials
- Tech Scout
- Unparalleled Data Quality
- Higher Quality Content
- 60% Fewer Hallucinations
Browse by: Latest US Patents, China's latest patents, Technical Efficacy Thesaurus, Application Domain, Technology Topic, Popular Technical Reports.
© 2025 PatSnap. All rights reserved.Legal|Privacy policy|Modern Slavery Act Transparency Statement|Sitemap|About US| Contact US: help@patsnap.com