Paraffin granulation underwater production method
A technology of underwater granulation and production methods, applied in the direction of wax physical treatment, etc., can solve the problems of low heat transfer coefficient, high energy consumption, and many hidden dangers of failure, etc., and achieve high pelleting pass rate, uniform particle size distribution, and smooth operation good effect
- Summary
- Abstract
- Description
- Claims
- Application Information
AI Technical Summary
Problems solved by technology
Method used
Image
Examples
Embodiment Construction
[0023] 1. According to figure 2 Explain the equipment structure of the granulator.
[0024] The function is to process the raw wax from liquid wax into granular wax. Mainly composed of three parts, from top to bottom are tower body 15-9, switch board 15-3, heat preservation board 15-2 and wax chamber 15-5.
[0025] Tower body: located on the upper part of the granulator, made of stainless steel. A circulating water inlet 15-1 is provided on the upper part of the tower body 15-9, and a water inlet tank is arranged in the tower body 15-9 on the side of the circulating water inlet 15-1, and an overflow edge is arranged in the water inlet tank; A water outlet tank and a cooling tank are provided, and the water outlet tank is partially opened; organic glass windows 15-6 are installed on both sides of the tower body.
[0026] The circulating water first enters the water inlet tank in the tower body 15-9 of the granulator 15, and the water flow is gently and evenly injected into t...
PUM
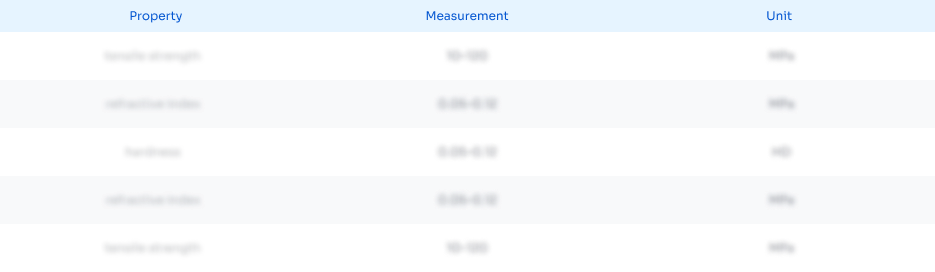
Abstract
Description
Claims
Application Information

- Generate Ideas
- Intellectual Property
- Life Sciences
- Materials
- Tech Scout
- Unparalleled Data Quality
- Higher Quality Content
- 60% Fewer Hallucinations
Browse by: Latest US Patents, China's latest patents, Technical Efficacy Thesaurus, Application Domain, Technology Topic, Popular Technical Reports.
© 2025 PatSnap. All rights reserved.Legal|Privacy policy|Modern Slavery Act Transparency Statement|Sitemap|About US| Contact US: help@patsnap.com