External rotor radial-axial three freedom degree mixed magnetic bearing
A hybrid magnetic bearing and external rotor technology, applied in the direction of the shaft and bearing, bearing, shaft, etc., can solve the problems of poor stability of magnetic bearings, small bearing capacity of magnetic bearings, etc., and achieve reduction in size, size, and power loss Effect
- Summary
- Abstract
- Description
- Claims
- Application Information
AI Technical Summary
Problems solved by technology
Method used
Image
Examples
Embodiment 1
[0027] Such as figure 1 As shown, an outer rotor radial-axial three-degree-of-freedom hybrid magnetic bearing includes a rotor 1, an axial stator 6 with a two-piece six-pole structure with 2 pieces × 3 poles, a radial stator 4, and a radial control coil 51, 52, 53, axial control coils 81, 82 and three permanent magnets 71, 72, 73. Each axial stator 6 on the left and right sides is composed of three axial stator poles 61, 62, 63 evenly distributed along the circumference, as figure 2 shown. A radial stator 4 with three magnetic poles evenly distributed along the circumference is located between two axial stators 6 . The three block-shaped circular permanent magnets 71, 72, and 73 are made of high-performance rare earth permanent magnet material NdFeB, have the same shape and size, are radially magnetized, and are embedded in three radial stator poles 41, 42, and 43. The radial and axial biasing fluxes 9 are simultaneously provided in the outer annular groove. An axial air ...
PUM
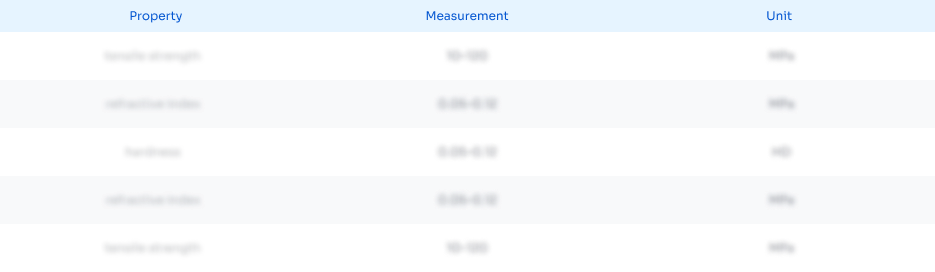
Abstract
Description
Claims
Application Information

- Generate Ideas
- Intellectual Property
- Life Sciences
- Materials
- Tech Scout
- Unparalleled Data Quality
- Higher Quality Content
- 60% Fewer Hallucinations
Browse by: Latest US Patents, China's latest patents, Technical Efficacy Thesaurus, Application Domain, Technology Topic, Popular Technical Reports.
© 2025 PatSnap. All rights reserved.Legal|Privacy policy|Modern Slavery Act Transparency Statement|Sitemap|About US| Contact US: help@patsnap.com