Low frequency modal vibration control apparatus and method for simulating bending and torsion for space sailboard
A torsional mode and bending technology, applied in mechanical oscillation control, non-electric variable control, computer control, etc., can solve the problems of high strain sensitivity, large deformation, and low control force, and achieve high strain sensitivity and large deformation , the effect of suppressing vibration
- Summary
- Abstract
- Description
- Claims
- Application Information
AI Technical Summary
Problems solved by technology
Method used
Image
Examples
Embodiment Construction
[0018] The present invention will be further described below in conjunction with the accompanying drawings and examples, but the protection scope of the present invention is not limited to the scope expressed by the examples.
[0019] Such as figure 1 , 2 , 3, the simulated space sailboard bending and torsional low-frequency modal vibration control device includes a mechanical support clamping device, a flexible cantilever plate 3, a bending mode shape memory alloy driver 1, a bending mode piezoelectric strain gauge sensor 2, One of the torsional mode shape memory alloy driver 4 and the second of the torsional mode shape memory alloy driver 6, resistance strain gauge combined sensor for detecting torsional mode 5, dynamic resistance strain gauge 7, multi-channel A / D conversion data acquisition Card 8, computer 9, liquid crystal display 13, I / O circuit board 10, switch drive circuit board 11 and high-power switching power supply 12; As a sensor to detect low-frequency modal v...
PUM
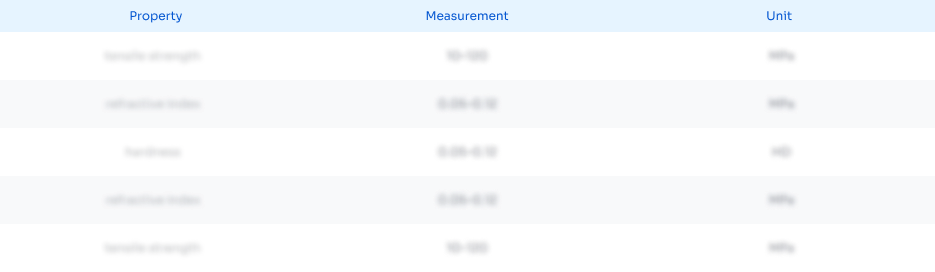
Abstract
Description
Claims
Application Information

- Generate Ideas
- Intellectual Property
- Life Sciences
- Materials
- Tech Scout
- Unparalleled Data Quality
- Higher Quality Content
- 60% Fewer Hallucinations
Browse by: Latest US Patents, China's latest patents, Technical Efficacy Thesaurus, Application Domain, Technology Topic, Popular Technical Reports.
© 2025 PatSnap. All rights reserved.Legal|Privacy policy|Modern Slavery Act Transparency Statement|Sitemap|About US| Contact US: help@patsnap.com