Harmless disposal method of waste diatomite containing sodium thiocyanate
A technology containing sodium thiocyanate and waste diatomite, applied in chemical instruments and methods, inorganic chemistry, silicon compounds, etc., can solve the problems of long process, large pressure drop, difficult to achieve harmlessness, etc. The effect of saving operation cost, simple process and less water consumption
- Summary
- Abstract
- Description
- Claims
- Application Information
AI Technical Summary
Problems solved by technology
Method used
Examples
Embodiment 1
[0022] Take 5kg of waste diatomaceous earth containing 8% sodium thiocyanate, add 2.5L of water according to the solid-liquid ratio of 1:0.5, stir in a 10L kettle for 5min, the total amount is 7.5kg, and transfer to a belt with a mesh diameter of 2μm On the filter cloth, the conveying speed of the filter cloth is 1m / min, and the vacuum degree of 0.04MPa is kept underneath. The filter is divided into 3 stages, the latter two stages are sprayed with water, and the spray water is 5L, the filtrate is collected in 3 stages, and the last stage is 2L. Separately collect and return to the kettle to stir the raw materials, and the waste diatomaceous earth is discharged at the end of the filter cloth conveying. The sodium thiocyanate content in the treated waste diatomaceous earth is 0.07%, which achieves harmless treatment and can be returned to the system as a filter aid Repeated use or used as building materials, roadbeds and other materials.
Embodiment 2
[0024] Take 100 kg of waste diatomaceous earth containing 4% sodium thiocyanate, add 200L of water according to the solid-liquid ratio of 1:2, mix in a 500L kettle for 10 minutes, transfer to a belt filter cloth with a mesh pore size of 8μm, and transmit the filter cloth The speed is 0.2m / min. The filtrate is continuously separated by maintaining a vacuum of 0.03MPa below, and the top of the filter cloth is continuously sprayed and washed with water. The spray water is 100L. The filtrate is collected in 4 stages. The last stage of filtrate 40L is returned to the mixing kettle and mixed with the next batch of raw materials. , The waste diatomaceous earth is discharged at the end of the filter cloth conveying. The sodium thiocyanate content in the waste diatomaceous earth after the above treatment is 0.01%, which can be reused in the system.
Embodiment 3
[0026] Take 100kg of waste diatomaceous earth containing 4% sodium thiocyanate, add 100L of water according to the solid-liquid ratio of 1:1, mix in a 500L kettle for 10min, transfer to a belt filter cloth with a mesh pore size of 12μm, and transmit the filter cloth The speed is 0.4m / min. The filtrate is continuously separated by maintaining a vacuum of 0.06MPa below, and the top of the filter cloth is continuously sprayed and washed with water. The spray water is 100L. The filtrate is collected in 3 stages. The last stage of filtrate 40L is returned to the mixing kettle and mixed with the next batch of raw materials. , The waste diatomite is discharged at the end of the filter cloth conveying. The sodium thiocyanate content in the waste diatomite after the above treatment is 0.04%, which can be recycled to the system for reuse.
PUM
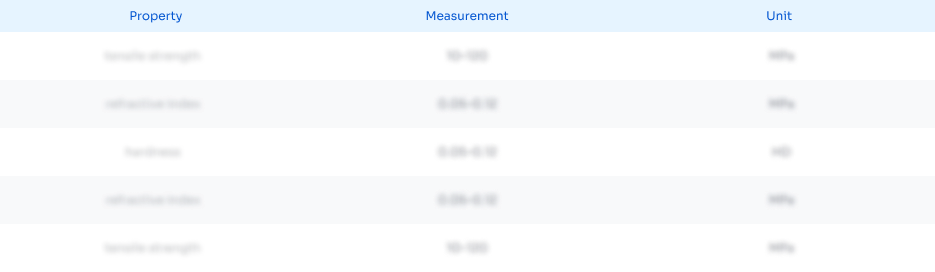
Abstract
Description
Claims
Application Information

- R&D
- Intellectual Property
- Life Sciences
- Materials
- Tech Scout
- Unparalleled Data Quality
- Higher Quality Content
- 60% Fewer Hallucinations
Browse by: Latest US Patents, China's latest patents, Technical Efficacy Thesaurus, Application Domain, Technology Topic, Popular Technical Reports.
© 2025 PatSnap. All rights reserved.Legal|Privacy policy|Modern Slavery Act Transparency Statement|Sitemap|About US| Contact US: help@patsnap.com