Method for preparing flyash cement
A technology of fly ash cement and fly ash, which is applied in the field of building materials, can solve the problems of low cement quality, unreasonable proportioning, use restrictions, etc., and achieve the effect of high quality, excellent quality and good benefit
- Summary
- Abstract
- Description
- Claims
- Application Information
AI Technical Summary
Problems solved by technology
Method used
Image
Examples
Embodiment 1
[0016] A. Preparation of clinker:
[0017] ①. First, take 8% of high loss on ignition fly ash, 2% of iron powder, 71% of limestone, 8% of sandstone siliceous raw material, 1% of steel slag and 10% of yellow coal by weight percentage; wherein high loss of ignition fly ash is AL 2 o 3 Fly ash with a content of 6.42% and a loss on ignition of more than 8%, SO in yellow coal 3 The content is 2.34%;
[0018] ②. Mix, pulverize and dry the above raw materials;
[0019] ③. Send the dried raw materials into the mill for fine grinding;
[0020] ④, and then transport the powdered material obtained after fine grinding to the continuous homogenization field for homogenization;
[0021] ⑤. Add water to the homogenized raw material to make a spherical body, send it to a kiln for calcination at a temperature of 1300-1400 °C, and then become clinker;
[0022] B. Preparation of finished products:
[0023] 1. Get 67% of the clinker prepared in step A, 32% of low loss on ignition fly ash a...
Embodiment 2
[0026] A. Preparation of clinker:
[0027] ①. First, take 9.5% high loss on ignition fly ash, 2.5% iron powder, 74% limestone, 5% sandstone siliceous raw material, 1% steel slag and 8% yellow coal by weight percentage; wherein high loss on ignition fly ash is AL 2 o 3 Fly ash with a content of 6.42% and a loss on ignition of more than 8%, SO in yellow coal 3 The content is 2.34%;
[0028] ②. Mix, pulverize and dry the above raw materials;
[0029] ③. Send the dried raw materials into the mill for fine grinding;
[0030] ④, and then transport the powdered material obtained after fine grinding to the continuous homogenization field for homogenization;
[0031] ⑤. Add water to the homogenized raw material to make a spherical body, send it to a kiln for calcination at a temperature of 1300-1400 °C, and then become clinker;
[0032] B. Preparation of finished products:
[0033] 1. Get 67% of the clinker prepared in step A, 30% of low ignition loss fly ash and 3% of gypsum wi...
Embodiment 3
[0036] A. Preparation of clinker:
[0037] ①, first take high loss on ignition fly ash 7%, iron powder 3%, limestone 72.5%, sandstone siliceous raw material 5%, steel slag 1.5% and yellow coal 11% by weight percentage; wherein high loss on ignition fly ash is AL 2 o 3 Fly ash with a content of 6.42% and a loss on ignition of more than 8%, SO in yellow coal 3 The content is 2.34%;
[0038] ②. Mix, pulverize and dry the above raw materials;
[0039] ③. Send the dried raw materials into the mill for fine grinding;
[0040] ④, and then transport the powdered material obtained after fine grinding to the continuous homogenization field for homogenization;
[0041] ⑤. Add water to the homogenized raw material to make a spherical body, send it to a kiln for calcination at a temperature of 1300-1400 °C, and then become clinker;
[0042] B. Preparation of finished products:
[0043] 1. Get 70% of the clinker prepared in step A, 27% of low loss on ignition fly ash and 3% of gypsum...
PUM
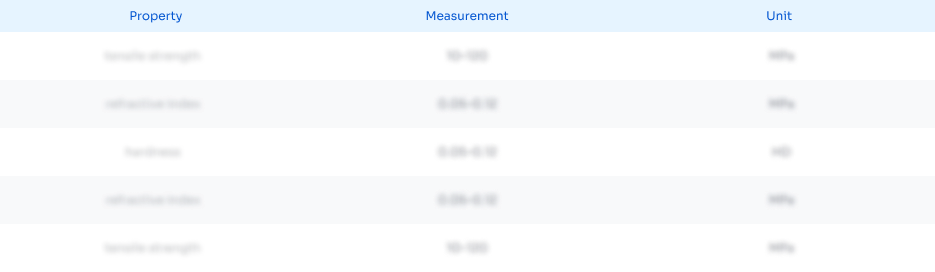
Abstract
Description
Claims
Application Information

- R&D Engineer
- R&D Manager
- IP Professional
- Industry Leading Data Capabilities
- Powerful AI technology
- Patent DNA Extraction
Browse by: Latest US Patents, China's latest patents, Technical Efficacy Thesaurus, Application Domain, Technology Topic, Popular Technical Reports.
© 2024 PatSnap. All rights reserved.Legal|Privacy policy|Modern Slavery Act Transparency Statement|Sitemap|About US| Contact US: help@patsnap.com