Two-dimension flexible hinge work bench of fiber optics displacement feedback closed-loop control
A flexible hinge, closed-loop control technology, applied in optics, optical components, optical devices, etc., can solve the problems of limited accuracy and positioning stability of flexible hinge worktables, and difficult to guarantee its own accuracy, to improve the dynamic test range and Sensitivity, free from electromagnetic interference, good electrical insulation performance
- Summary
- Abstract
- Description
- Claims
- Application Information
AI Technical Summary
Problems solved by technology
Method used
Image
Examples
Embodiment Construction
[0019] see Figure 1~3 , the present invention is provided with two-dimensional flexible hinge platform 1 (consisting of platform base 12 and mobile platform 11), transverse piezoelectric ceramic driver 2, longitudinal piezoelectric ceramic driver 3, transverse optical fiber displacement sensor (not shown in the figure) and longitudinal Optical fiber displacement sensor (not shown in the figure). The two-dimensional flexible hinge platform 1 is provided with a transverse installation hole 111 on the transverse centerline and a longitudinal installation hole 112 on the longitudinal centerline, as well as a transverse fiber installation channel 13 and a longitudinal fiber installation channel 14 . The transverse optical fiber displacement sensor is provided with a main body and a transverse optical fiber, and the longitudinal optical fiber displacement sensor is provided with a main body and a longitudinal optical fiber. The horizontal optical fiber and the vertical optical fib...
PUM
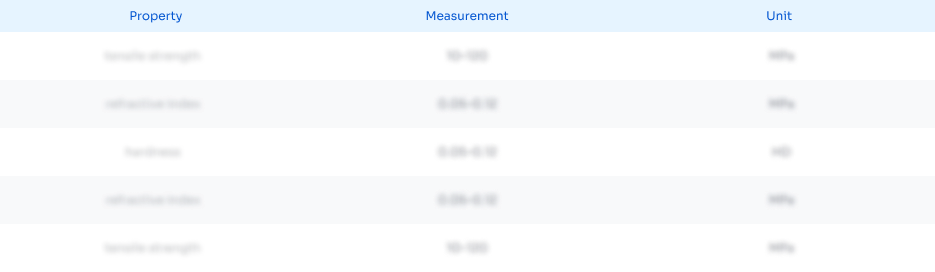
Abstract
Description
Claims
Application Information

- Generate Ideas
- Intellectual Property
- Life Sciences
- Materials
- Tech Scout
- Unparalleled Data Quality
- Higher Quality Content
- 60% Fewer Hallucinations
Browse by: Latest US Patents, China's latest patents, Technical Efficacy Thesaurus, Application Domain, Technology Topic, Popular Technical Reports.
© 2025 PatSnap. All rights reserved.Legal|Privacy policy|Modern Slavery Act Transparency Statement|Sitemap|About US| Contact US: help@patsnap.com