Press felt for papermaking
A technology for pressing felts and wool layers, which is applied in papermaking, papermaking machines, textiles and papermaking, etc. It can solve the problems of volume expansion and rewetting, and achieve smoothness maintenance, depilation resistance and abrasion resistance, and paper product quality improvement. Effect
- Summary
- Abstract
- Description
- Claims
- Application Information
AI Technical Summary
Problems solved by technology
Method used
Image
Examples
preparation example Construction
[0042] When hot pressing is performed in the production process of the press felt, the sheath component melts, thereby causing fiber shrinkage of the core-sheath composite fibers 41, and accompanying this, the base side batt layer 22 and the wet paper contact side batt layer 21 become dense, so the felt Surface smoothness is improved.
[0043] After the base side batt layer 22 and the wet paper contact side batt layer 21 become dense, when the press felt 10 is out of the nip pressure, the moisture in the press side batt layer 23 is difficult to move because the dense layer forms a barrier, thus effectively inhibiting rewetting phenomenon.
[0044] In the present invention, the batt layer 21 on the wet paper contact side does not contain the core-sheath composite fiber 41 but is composed of normal nylon fibers 42 , and only the core-sheath composite fiber 41 is contained in the structure of the base side batt layer 22 . Therefore, smoothness, depilation and abrasion resistance...
Embodiment
[0063] The first embodiment of the press felt for papermaking of the present invention will be specifically described by the following examples. However, the present invention is not limited to these Examples.
[0064] Preparation of core-sheath composite fibers;
[0065] Prepare refined nylon 6 (caprolactam: melting point 220°C) and copolymerized nylon 6 / 12 (caprolactam / laurolactam: melting point 140°C), put them into separate extruders with devolatilization ports, and then Remove the volatile matter in the middle, and the melted core material nylon 6 and the sheath material copolymerized nylon 6 / 12 are quantified with a quantitative gear pump in a melted state, and supplied to each core-sheath composite spinning nozzle. After passing through the core-sheath composite spinning nozzle, the core-sheath composite fiber spun into silk is cooled in the air cylinder, oiled at the same time, wound at a natural stretch ratio, and then cut to a fixed length after stretching and crimp...
PUM
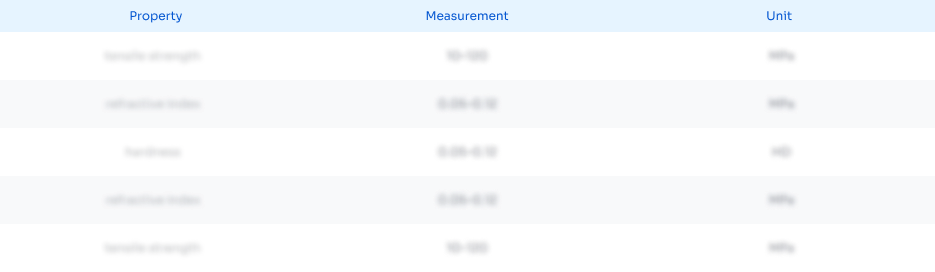
Abstract
Description
Claims
Application Information

- Generate Ideas
- Intellectual Property
- Life Sciences
- Materials
- Tech Scout
- Unparalleled Data Quality
- Higher Quality Content
- 60% Fewer Hallucinations
Browse by: Latest US Patents, China's latest patents, Technical Efficacy Thesaurus, Application Domain, Technology Topic, Popular Technical Reports.
© 2025 PatSnap. All rights reserved.Legal|Privacy policy|Modern Slavery Act Transparency Statement|Sitemap|About US| Contact US: help@patsnap.com