Sintered ring cold exhaust heat stepped recovery power generation system and technique
A technology of cascade recovery and power generation system is applied in the field of sintering waste heat utilization, which can solve the problems of low power generation steam parameters, large heat dissipation loss of hot air, low heat exchange efficiency, etc. Improve the effect of steam parameters
- Summary
- Abstract
- Description
- Claims
- Application Information
AI Technical Summary
Problems solved by technology
Method used
Image
Examples
Embodiment Construction
[0017] The present invention will be further described below in conjunction with the accompanying drawings.
[0018] See attached figure 1 , The sintering ring cooling waste heat cascade recovery power generation system of the present invention, the sintering ring cooling machine 1 inlet ore temperature is 750-850°C, and the sintering ore outlet temperature of the third stage drops to 350°C. The temperature of the large circulating air at the outlet of the waste heat boiler 6 is about 150°C, and then enters the upper air chamber 2 of the third sintering ore, and heat exchangers 4 are arranged above the third and second sintering ores, and the hot air sub-circulations are respectively heated and exchanged. Heater, after the large circulating air is heated, it enters the second section and the first section upwind room through the baffle in turn, and then merges with the first section circulating hot air to enter the waste heat boiler 6, and the air temperature entering the wast...
PUM
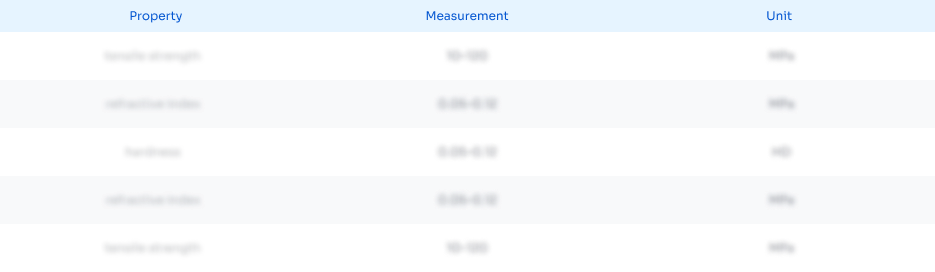
Abstract
Description
Claims
Application Information

- R&D
- Intellectual Property
- Life Sciences
- Materials
- Tech Scout
- Unparalleled Data Quality
- Higher Quality Content
- 60% Fewer Hallucinations
Browse by: Latest US Patents, China's latest patents, Technical Efficacy Thesaurus, Application Domain, Technology Topic, Popular Technical Reports.
© 2025 PatSnap. All rights reserved.Legal|Privacy policy|Modern Slavery Act Transparency Statement|Sitemap|About US| Contact US: help@patsnap.com