Cable terminal bonding machine
A technology of pressing machine and pressing mechanism, which is applied in circuit/collector parts, electrical components, circuits, etc., can solve the problems of low qualification rate, hidden dangers of occupational diseases of employees, and long time of skilled operation of new operators. The effect of high rate and avoiding occupational diseases of employees
- Summary
- Abstract
- Description
- Claims
- Application Information
AI Technical Summary
Problems solved by technology
Method used
Image
Examples
Embodiment Construction
[0023] The specific implementation manner of the present invention will be described in detail below in conjunction with the accompanying drawings and preferred embodiments.
[0024] As shown in the figure, a cable terminal pressing machine includes a terminal feeding mechanism 1, a terminal pressing mechanism 2, and a cable clamping fixture 3, a cam mechanism 4, a branching mechanism 5, a stepping mechanism 6 and a working table 7. The cam mechanism is composed of a cam bracket 4-1, a cam 4-2, a bump 4-3 and a bracket guide rail 4-4. Frame 4-6 is fixed on one side of the support, and the support and the guide rail of the support are slidably matched, and the guide rail of the support is fixed on the worktable. A fixing groove 4-7 is provided above the cam support, which is pinned to the double ears 4-8 on the cam support. The upper end of the cam fixing plate 4-9 is inserted into the fixing groove and is plugged in or separated from the cam notch 4-10, and the corresponding ...
PUM
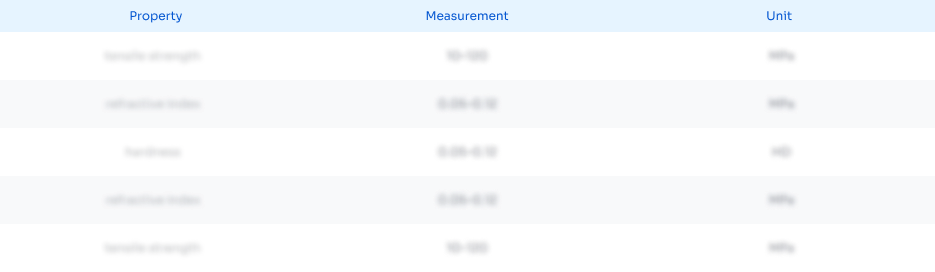
Abstract
Description
Claims
Application Information

- R&D Engineer
- R&D Manager
- IP Professional
- Industry Leading Data Capabilities
- Powerful AI technology
- Patent DNA Extraction
Browse by: Latest US Patents, China's latest patents, Technical Efficacy Thesaurus, Application Domain, Technology Topic, Popular Technical Reports.
© 2024 PatSnap. All rights reserved.Legal|Privacy policy|Modern Slavery Act Transparency Statement|Sitemap|About US| Contact US: help@patsnap.com