Hydraulic shock vibration system in multifunctional engineering equipment
A technology of engineering equipment and hydraulic impact, applied in drilling equipment, impact drilling, drilling equipment and methods, etc., to achieve the effect of reducing cost and improving operation efficiency
- Summary
- Abstract
- Description
- Claims
- Application Information
AI Technical Summary
Problems solved by technology
Method used
Image
Examples
Embodiment Construction
[0012] It is realized by installing other working heads successively on the excavator substrate, referring to Fig. 1, it has the excavator substrate 6, it also has the bucket 2 of the down-the-hole drill bit 3, the excavator, the frozen soil drill rod and the hydraulic pressure Hammer 11, lug plate 4 is arranged on the bucket of excavator, down-the-hole drill bit, permafrost drilling rod and hydraulic hammer, is installed on the forearm 6.1 of excavator by bolt, and it is also provided with hydraulic output oil circuit to submersible. Hole drilling bits, frozen soil drilling rods and hydraulic hammers, see figure 2 , it superimposes the general valve on the original hydraulic system, and uses the advanced pilot principle to control the operating system in order to avoid malfunction. figure 2 Among them, 10 is the rock drilling machine, 11 is the blowing pipe, 12 is the control valve, 13 is the radiator, 14 is the oil tank, 15 is the valve group, 16 is the pump group, 17 is the...
PUM
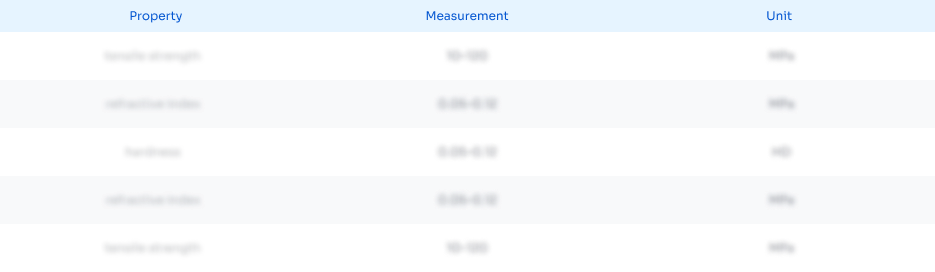
Abstract
Description
Claims
Application Information

- R&D
- Intellectual Property
- Life Sciences
- Materials
- Tech Scout
- Unparalleled Data Quality
- Higher Quality Content
- 60% Fewer Hallucinations
Browse by: Latest US Patents, China's latest patents, Technical Efficacy Thesaurus, Application Domain, Technology Topic, Popular Technical Reports.
© 2025 PatSnap. All rights reserved.Legal|Privacy policy|Modern Slavery Act Transparency Statement|Sitemap|About US| Contact US: help@patsnap.com