Polychloroethylene / organic modified sheet silicate nano-composite material
A technology of nanocomposite materials and layered silicate, which is applied in the field of nanocomposite materials and its preparation, can solve the problems of no significant improvement in the performance of PVC, achieve the effects of increasing added value, simple production process, and improving thermal stability
- Summary
- Abstract
- Description
- Claims
- Application Information
AI Technical Summary
Problems solved by technology
Method used
Image
Examples
Embodiment 1
[0038] Mix 100g of PVC resin with 3g of organotin stabilizer, 1.0g of lubricant, and 2g of other additives in a high-speed mixer, discharge at about 110°C, and then mix the mixture with 1g of unmodified sodium montmorillonite (MMT) Melt and blend on a twin-roller plastic mixer at a temperature of about 170°C. After 8 minutes, the sheet is produced, and then molded into 1mm and 4mm plates on a semi-automatic pressure molding machine at about 185°C, and cut into samples for use.
[0039]The interlayer spacing of montmorillonite in the sample was measured by WAXD, and the samples were analyzed by scanning electron microscope and transmission electron microscope. The results showed that most of the sodium-based montmorillonite was dispersed in the PVC matrix in the form of agglomerated particles, indicating that the PVC macromolecules were not Intercalation into the montmorillonite layer, sodium montmorillonite and PVC just form a common blended composite material. The performance...
Embodiment 2
[0043] Add 5g of PVC resin, 10g of unmodified sodium montmorillonite (MMT) and 15g of organic modifier polyoxyethylene-polyoxypropylene copolymer (EP) into 50 grams of tetrahydrofuran solvent, stir for about 2h; then evaporate tetrahydrofuran solvent to obtain organically modified montmorillonite.
[0044] Mix 100g of polyvinyl chloride resin with 3g of organotin stabilizer, 0.5g of lubricant, and 1.0g of other additives in a high-speed mixer, discharge at about 110°C, and then mix the mixture with the above-mentioned organic modified montmorillonite 2.5g is melted and blended on a twin-roller plastic mixer at a temperature of about 170°C, and the sheet is released after 8 minutes, and then molded into 1mm and 4mm plates on a semi-automatic pressure molding machine at 185°C, and cut into samples for use.
[0045] WAXD was used to measure the layer spacing of montmorillonite in the material, and the samples were analyzed by scanning electron microscope and transmission electron...
Embodiment 3
[0049] Dilute the coupling agent KH-560 and ethanol by 1:10, take the coupling agent (the amount is 1% of the weight of illite) and illite in a high-speed mixer, stir and blend them, and put them in an oven at about 100°C to dry for about 1h, discharge and set aside.
[0050] Mix 100g of polyvinyl chloride resin with 5g of organotin stabilizer, 2g of lubricant, and 2g of other additives in a high-speed mixer, discharge at about 110°C, and then mix the mixture with 3g of coupling agent modified illite Melt and blend on a twin-roller plastic mixer with a temperature of about 170°C. After 8 minutes, the sheet is released, and then molded into 1mm and 4mm plates on a semi-automatic pressure molding machine at about 185°C, and cut into samples for use.
[0051] The layer spacing of illite in the material was measured by WAXD, and the samples were analyzed by scanning electron microscope and transmission electron microscope. The dispersibility of stone in PVC matrix, the performanc...
PUM
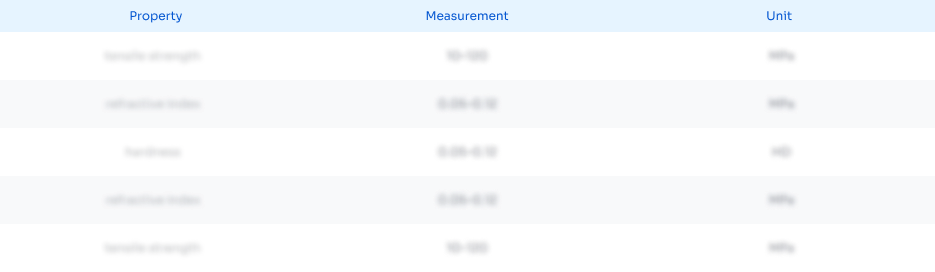
Abstract
Description
Claims
Application Information

- R&D
- Intellectual Property
- Life Sciences
- Materials
- Tech Scout
- Unparalleled Data Quality
- Higher Quality Content
- 60% Fewer Hallucinations
Browse by: Latest US Patents, China's latest patents, Technical Efficacy Thesaurus, Application Domain, Technology Topic, Popular Technical Reports.
© 2025 PatSnap. All rights reserved.Legal|Privacy policy|Modern Slavery Act Transparency Statement|Sitemap|About US| Contact US: help@patsnap.com