Pipes shaping limit curve test device for hydraulic bulging process
A forming limit curve and hydraulic bulging technology, which is applied in the field of mechanical engineering, can solve problems such as the inability to effectively realize the linear strain path, the inability to change the strain state, and the inability to obtain the forming limit curve.
- Summary
- Abstract
- Description
- Claims
- Application Information
AI Technical Summary
Problems solved by technology
Method used
Image
Examples
Embodiment 1
[0018] The device in this embodiment is an experimental device for measuring the forming limit curve under tension-compression strain state, and can measure the forming limit of the material when the strain ratio varies between -1 and 0.
[0019] Such as figure 1 and figure 2 Shown, the present embodiment is made up of patrix, counterdie and push rod.
[0020] Upper die is made up of upper connecting plate 1 and upper insert 2. The upper connecting plate 1 is connected to the hydraulic bulging machine by screws. The upper insert 2 is connected with the upper connecting plate 1 by screws, the lower surface thereof is a plane, and there is no transition fillet between the bottom surface and the side surface.
[0021] Lower mold is made up of fixed block 3, lower insert 6 and lower mold 7. Lower mold 7 is fixed on the workbench of hydraulic bulging machine. The lower insert 6 is arranged in the cavity of the lower mold 7 . There are two fixed blocks 3 connected to the lowe...
Embodiment 2
[0036] This embodiment is an experimental device for measuring the forming limit curve under the state of tension-tension strain, which can measure the forming limit of the material when the strain ratio varies between 0 and 1.
[0037] Such as figure 1 and figure 2 Shown, the present embodiment is made up of patrix, counterdie and push rod.
[0038] The upper die is composed of an upper connecting plate 1 and an upper insert 2, and the upper connecting plate 1 is connected to the hydraulic bulging machine by screws. The upper insert 2 is connected with the upper connecting plate 1 by screws, the lower surface thereof is a plane, and there is a transitional fillet between the bottom surface and the side surface.
[0039]Lower mold is made up of fixed block 3, lower insert 6 and lower mold 7. Lower mold 7 is fixed on the workbench of hydraulic bulging machine. The lower insert 6 is arranged in the cavity of the lower mold 7 . There are two fixed blocks 3 connected to the ...
PUM
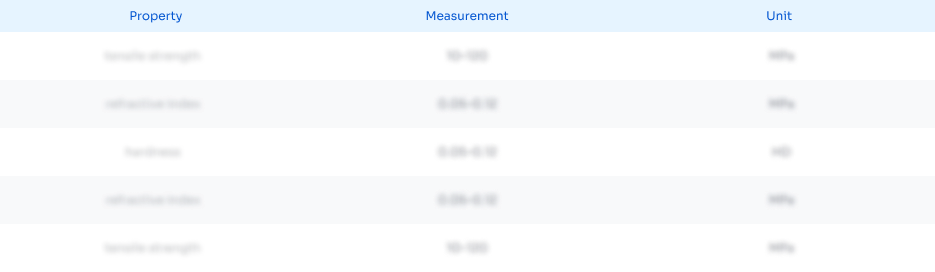
Abstract
Description
Claims
Application Information

- R&D
- Intellectual Property
- Life Sciences
- Materials
- Tech Scout
- Unparalleled Data Quality
- Higher Quality Content
- 60% Fewer Hallucinations
Browse by: Latest US Patents, China's latest patents, Technical Efficacy Thesaurus, Application Domain, Technology Topic, Popular Technical Reports.
© 2025 PatSnap. All rights reserved.Legal|Privacy policy|Modern Slavery Act Transparency Statement|Sitemap|About US| Contact US: help@patsnap.com